The lifespan of an offshore container begins with its design and fabrication. Offshore containers are typically built according to DNV-ST-E271 (formerly DNV 2.7-1) or other equivalent offshore standards, which impose stringent structural and safety requirements. The design process accounts for dynamic lifting forces, impact resistance, and corrosion protection, ensuring that the container can withstand frequent handling and the unpredictable nature of offshore operations. High-quality offshore containers are constructed from thick structural steel with reinforced frames, providing both mechanical strength and durability. The use of certified welding techniques and quality-controlled materials during manufacturing plays a critical role in the container’s long-term performance, as poorly fabricated joints or inferior steel can significantly reduce lifespan.
Once deployed, the operating environment becomes the dominant factor affecting the longevity of offshore containers. Offshore containers are continuously subjected to marine corrosion, temperature fluctuations, and abrasive wear from cargo loading and unloading. Saltwater exposure accelerates the degradation of untreated steel surfaces, making protective coatings and galvanization essential for long-term durability. Even the best coatings will gradually wear down over time, especially in areas subject to frequent handling or impact, such as corner fittings, door frames, and padeyes. Containers operating in tropical climates or areas with high humidity face an even greater risk of corrosion, shortening their service life without proper maintenance.
The intensity and frequency of use also have a direct impact on the lifespan of an offshore container. Containers used for daily cargo transport in offshore supply chains are exposed to more lifting operations, loading stresses, and environmental wear than those used intermittently for storage or specialized applications. Repeated lifting, particularly in rough sea states, places significant strain on structural components and lifting points. Over time, welded joints, padeyes, and sling attachment points become critical failure areas, especially if not properly inspected and maintained. Impact damage during handling, whether from crane operations or accidental collisions, further accelerates structural degradation.
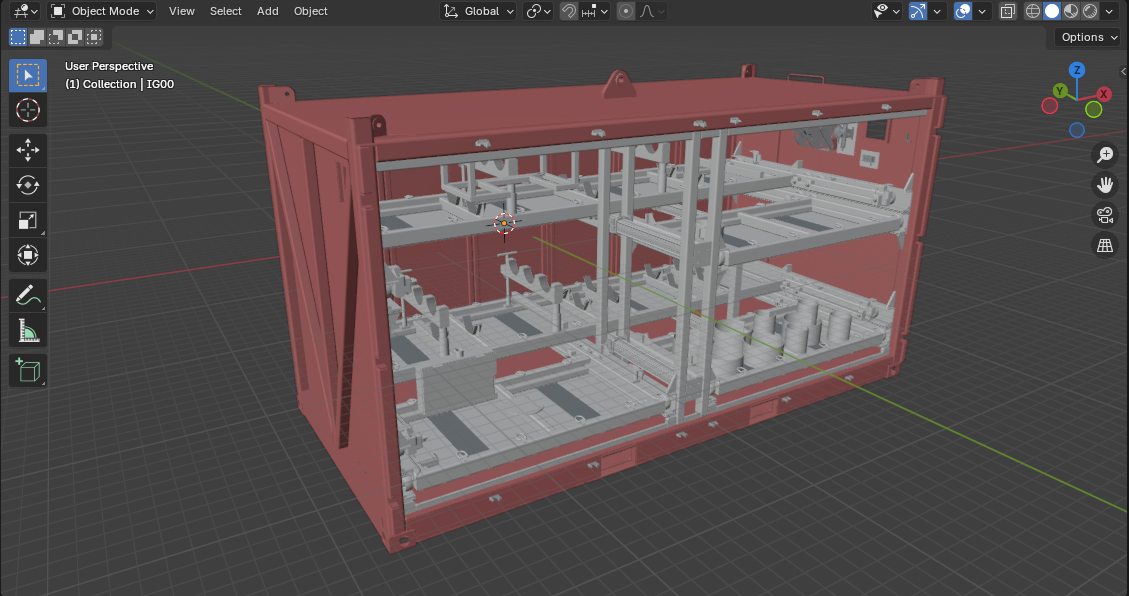
Regular inspection and maintenance practices are vital for prolonging the service life of offshore containers. Offshore regulations require periodic inspections, typically every 6 to 12 months, to assess structural integrity, lifting points, and corrosion protection. These inspections involve non-destructive testing (NDT) techniques such as magnetic particle inspection or ultrasonic testing to detect cracks and hidden defects. Containers that pass inspection receive certification for continued use, while those that show significant wear or damage must undergo repairs or be withdrawn from service. Preventive maintenance, such as repainting, seal replacement, and component reconditioning, can significantly extend the container’s lifespan, particularly in harsh environments. However, poorly maintained containers often degrade quickly, making regular upkeep not just a regulatory obligation but also a cost-effective investment.
The lifespan of an offshore container is further influenced by how well it complies with changing safety and operational standards. Offshore certification bodies such as DNV, Lloyd’s Register, and Bureau Veritas regularly update their requirements to reflect new safety technologies and industry best practices. Containers that meet the latest certification standards tend to have a longer service life, as they are built to withstand more demanding operational conditions. Conversely, older containers designed under outdated standards may become non-compliant or unsafe for offshore use, requiring costly modifications or decommissioning.
Despite all preventive measures, the natural degradation of materials and the cumulative effects of operational stresses ultimately define the finite lifespan of an offshore container. Under typical offshore conditions, a well-maintained offshore container can last between 10 and 15 years, although some containers may remain in service for up to 20 years with exceptional care and moderate use. Containers exposed to extreme environments or high-intensity operations, however, may require replacement after only 5 to 10 years. Once a container reaches the end of its operational life, it is either decommissioned, recycled for materials, or repurposed for non-critical applications.
In summary, the lifespan of an offshore container is not simply a function of time but rather the outcome of design quality, environmental exposure, operational intensity, and maintenance practices. While high-quality materials and robust design can provide the foundation for longevity, regular inspections, protective treatments, and compliance with safety standards are what ultimately determine how long an offshore container remains fit for service. For offshore operators, maximizing the lifespan of containers is not only a matter of cost efficiency but also a critical aspect of maintaining safety and minimizing the risk of cargo loss or operational downtime in challenging offshore environments.