In the challenging and often unforgiving environment of offshore operations, the choice of material for offshore containers is a critical decision that directly impacts their performance, durability, and safety. Offshore containers are subjected to extreme conditions, including saltwater exposure, high winds, heavy rainfall, and temperature fluctuations. These conditions demand materials that can withstand corrosion, mechanical stress, and environmental degradation while maintaining structural integrity over extended periods.
Corrosion-Resistant Steel:
Corrosion-resistant steel, particularly grades such as Corten steel, is widely regarded as the industry standard for offshore containers. This material is specifically designed to resist corrosion, making it highly suitable for the saline and humid conditions prevalent in offshore environments. Corten steel forms a protective rust-like layer when exposed to the elements, which acts as a barrier against further corrosion. This self-protecting characteristic significantly enhances the longevity of the container, reducing the need for frequent maintenance and repairs. Additionally, corrosion-resistant steel offers excellent mechanical strength, ensuring that the container can withstand the physical stresses associated with offshore operations, such as heavy loads and rough handling.
While suitable from a point of view of corrosion resistance, this type of material is generally not used in offshore applications, for a number of reasons.
Aluminum: Lightweight and Durable
Aluminum is another material commonly used in the construction of offshore containers, particularly when weight reduction is a priority. Aluminum containers are significantly lighter than their steel counterparts, making them easier to transport and handle. Despite their reduced weight, aluminum containers offer impressive durability and resistance to corrosion. Aluminum naturally forms a thin oxide layer when exposed to air, which protects the underlying material from further oxidation. This inherent corrosion resistance makes aluminum a viable option for offshore environments. However, it is important to note that aluminum containers may not offer the same level of mechanical strength as steel containers, which can be a consideration for applications involving heavy loads or extreme mechanical stress.
Stainless Steel: Premium Performance
Stainless steel is another material that offers exceptional performance in extreme offshore conditions. Known for its superior corrosion resistance, stainless steel contains chromium, which forms a passive layer of chromium oxide on the surface, preventing further oxidation. This material is highly resistant to saltwater, chemicals, and environmental degradation, making it an excellent choice for offshore containers. Stainless steel also provides excellent mechanical strength and durability, ensuring that the container can withstand the rigors of offshore operations. However, stainless steel is generally more expensive than other materials, which can be a consideration for cost-sensitive projects. Despite the higher initial cost, the long-term benefits of reduced maintenance and extended service life often justify the investment.
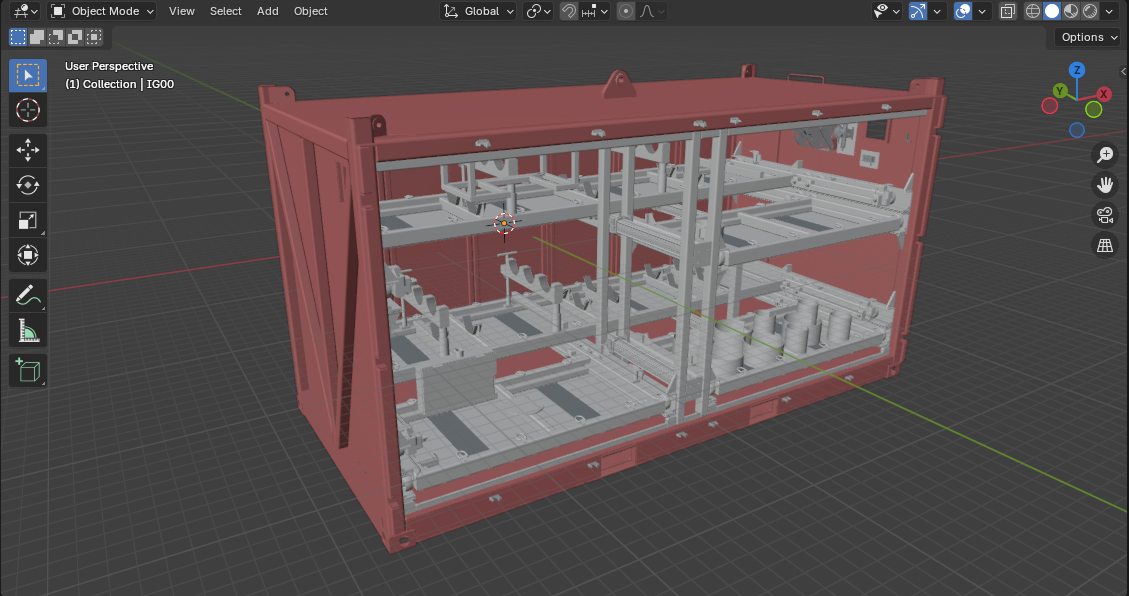
Coatings and Surface Treatments: Enhancing Material Performance
In addition to the base material, coatings and surface treatments play a crucial role in enhancing the performance of offshore containers in extreme conditions. Protective coatings, such as epoxy, polyurethane, and zinc-rich paints, can be applied to steel and aluminum containers to provide an additional layer of protection against corrosion and environmental degradation. These coatings act as a barrier, preventing direct contact between the material and corrosive elements. Surface treatments, such as anodizing for aluminum, can also improve corrosion resistance and durability. The choice of coating or surface treatment depends on the specific environmental conditions and performance requirements of the container.
Conclusion
Selecting the best material for offshore containers in extreme conditions involves a careful consideration of factors such as corrosion resistance, mechanical strength, weight, and cost. Corrosion-resistant steel, particularly Corten steel, remains the industry standard due to its excellent balance of durability and cost-effectiveness. Aluminum offers a lightweight alternative with good corrosion resistance, while composite materials provide advanced solutions with tailored properties. Stainless steel, though more expensive, offers premium performance and long-term benefits.
Additionally, protective coatings and surface treatments can further enhance the performance of these materials.
Ultimately, the choice of material should be guided by the specific requirements of the offshore operation, ensuring that the container can withstand the extreme conditions and deliver reliable performance over its service life.