MEPC 80, held in July 2023, discussed amendments to MARPOL Annex V regarding the discharge of garbage from ships. One of the key topics was the consideration of new technologies for onboard waste treatment, including devices that use mechanical friction to convert waste into a sterile, dehydrated biomass.
The mechanical friction waste treatment process involves the following steps:
a) Waste Collection and Loading:
- Various types of organic waste (food waste, sewage sludge) are collected and loaded into the treatment unit.
b) Mechanical Shredding:
- Waste is shredded into smaller particles to increase surface area and facilitate treatment.
c) Friction-Based Treatment:
- The shredded waste is subjected to intense mechanical friction within a sealed chamber.
- This friction generates heat, typically reaching temperatures of 120-150°C.
d) Dehydration and Sterilization:
- The heat generated by friction causes rapid evaporation of moisture from the waste.
- The high temperature also sterilizes the waste, eliminating pathogens and harmful bacteria.
e) Biomass Production:
- The end result is a dry, sterile biomass, significantly reduced in volume (up to 90% reduction).
f) Vapor Treatment:
- Water vapor produced during the process is condensed and treated before discharge.
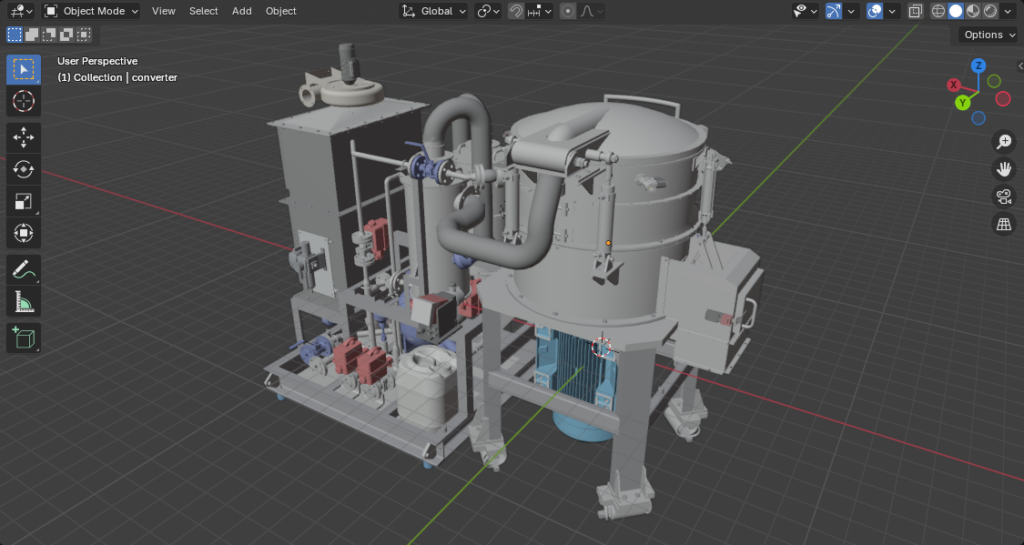
This mechanical friction-based waste treatment technology represents a promising alternative to traditional incineration or storage methods, aligning with the maritime industry’s goals of reducing environmental impact and improving onboard waste management.
The following considerations are key to understand this technology and its potential applications:
- Key Advantages:
- No external heat source required, improving energy efficiency
- Significant volume reduction of waste
- Production of sterile biomass that may be suitable for discharge or use as a resource
- No chemicals or additives needed in the process
- Regulatory Considerations (MEPC 80):
- The committee recognized the potential of such technologies to reduce marine pollution.
- Discussions focused on developing guidelines for the approval and operation of these devices.
- Emphasis was placed on ensuring that the discharged material meets environmental standards.
- Operational Aspects:
- The process is typically batch-operated, with cycle times of 3-6 hours depending on waste composition.
- Energy consumption is generally lower compared to incineration-based systems.
- Regular maintenance is required, particularly for the mechanical components subject to wear.
- Challenges and Considerations:
- Ensuring consistent performance across various waste types and compositions
- Developing standardized testing procedures to verify environmental compliance of the end product
- Integration with existing waste management systems onboard ships
- Future Outlook:
- Further refinement of the technology is expected to improve efficiency and reduce maintenance requirements.
- Development of comprehensive guidelines by IMO for approval and operation of such devices.
- Potential for wider adoption as ships seek more sustainable waste management solutions.
- Key Advantages:

We can provide the following engineering services associated with the design and installation of a thermal waste treatment device.
- Feasibility Study and Concept Design:
- Evaluation of space availability and weight considerations
- Preliminary process flow diagrams
- Conceptual layout designs
- Initial cost estimates and project timeline
- Detailed Engineering Design:
- Process engineering and equipment sizing
- Piping and Instrumentation Diagrams (P&IDs)
- 3D modeling of the equipment layout
- Electrical system design and integration
- Equipment Specification and Procurement Support:
- Development of technical specifications for major equipment
- Vendor evaluation and selection assistance
- Review of vendor documentation and drawings
- Structural Modifications Design:
- Reinforcement designs for existing structures if required
- Finite Element Analysis (FEA) for critical structural components
- Integration Engineering:
- Interface design with existing ship systems (e.g., power, water)
- Modification of existing piping systems
- Safety and Risk Engineering:
- Failure Mode and Effects Analysis (FMEA)
- Regulatory Compliance and Classification:
- Liaison with classification societies
- Preparation of documentation for class approval
- Development of procedures to meet regulatory requirements
- Installation Planning:
- Development of detailed installation procedures
- Creation of work packages for shipyard or offshore installation
- Lift plans for major equipment
- Installation sequence optimization
- Commissioning and Start-up Support:
- Development of commissioning procedures
- Supervision of installation and commissioning activities
- Performance of system tests and trials
- Troubleshooting and optimization support
- Documentation and Training:
- Preparation of operating and maintenance manuals
- Development of crew training programs
- Environmental Impact Assessment:
- Analysis of the thermal waste treatment system’s environmental benefits
- Support for environmental permit applications
- Project Management:
- Overall project scheduling and coordination
- Cost control and progress reporting
- Quality assurance and control
- Lifecycle Support:
- Development of maintenance and inspection schedules
- Optimization studies for long-term operation
- Technical support for system upgrades or modifications
- Feasibility Study and Concept Design:
This mechanical friction-based waste treatment technology represents a promising alternative to traditional incineration or storage methods, aligning with the maritime industry’s goals of reducing environmental impact and improving onboard waste management.