Offshore modular solutions have emerged as a critical component in the oil and gas industry, providing increased flexibility, efficiency, and cost-effectiveness in the development and operation of offshore facilities. These solutions encompass a wide range of prefabricated, self-contained units that can be rapidly deployed, relocated, and repurposed to meet the dynamic demands of offshore exploration and production.
The adoption of modular technology has been driven by the necessity for enhanced project execution efficiency. Traditional offshore construction methods often involve significant logistical challenges, extended lead times, and high capital expenditures. Modular solutions mitigate these constraints by enabling fabrication in controlled environments, where quality control is more stringent and timelines are less susceptible to weather-related disruptions. This off-site construction methodology allows for parallel processing, whereby modules are built simultaneously with site preparation, resulting in a significant reduction in project schedules.
Safety and operational reliability are paramount in offshore environments, and modular solutions offer advantages in this regard. Since modular units are constructed in specialized facilities with rigorous quality assurance protocols, they tend to exhibit higher build consistency and structural integrity compared to conventional on-site assembly. Moreover, these units are designed to integrate seamlessly with existing offshore infrastructure, ensuring minimal disruption during installation and commissioning. The modular approach also reduces the need for extensive on-site labor, thereby decreasing the exposure of personnel to hazardous offshore conditions.
Flexibility and scalability are intrinsic benefits of offshore modular solutions. Operators can tailor modular installations to accommodate varying production capacities, environmental conditions, and regulatory requirements. For instance, in deepwater and ultra-deepwater developments, modular units can be adapted for floating production storage and offloading (FPSO) vessels, enhancing operational efficiency in remote and technically challenging locations. Similarly, in marginal field developments, modular platforms provide a cost-effective alternative to traditional fixed structures, allowing operators to optimize asset utilization and extend field life.
The economic advantages of modular solutions are further underscored by their reusability and ease of decommissioning. Unlike conventional offshore infrastructure, which often requires extensive dismantling and disposal, modular units can be repurposed for different projects or redeployed to alternative locations with minimal refurbishment. This adaptability not only contributes to cost savings but also aligns with the industry’s increasing focus on sustainability and environmental responsibility.
Integration with digitalization and automation technologies is another evolving aspect of offshore modular solutions. Modern modular units are increasingly equipped with smart sensors, real-time monitoring systems, and remote operation capabilities, enhancing operational oversight and predictive maintenance. This convergence of modularization and digitalization supports data-driven decision-making, reduces downtime, and optimizes asset performance over the lifecycle of an offshore facility.
In conclusion, offshore modular solutions represent a transformative approach to the development and operation of oil and gas infrastructure. Their ability to enhance efficiency, improve safety, and provide economic and environmental benefits positions them as a vital strategy in the evolving offshore energy landscape. As the industry continues to navigate challenges such as cost pressures, regulatory compliance, and the transition towards lower-carbon operations, modularization will play an increasingly pivotal role in shaping the future of offshore oil and gas developments.
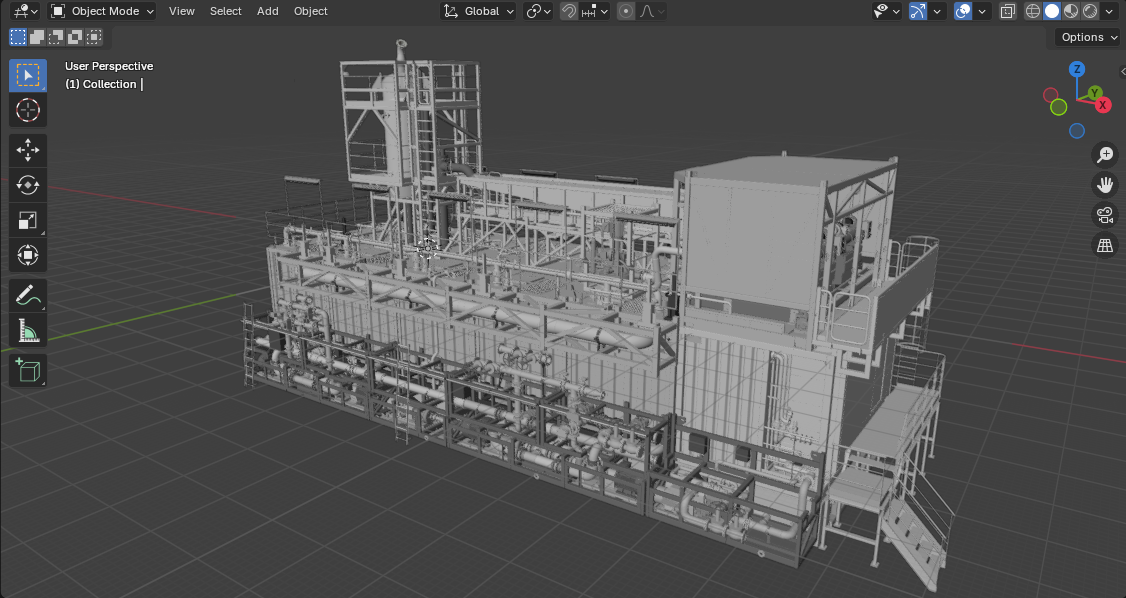
Fundamental Principles
Modularization in offshore oil and gas represents a sophisticated approach to facility design and construction that subdivides complex processing systems into manageable, pre-fabricated units. This methodology has evolved from simple package units to integrated systems that encompass complete process trains. The primary driving forces behind modularization include schedule optimization, quality control enhancement, and cost reduction through parallel construction activities.
Economic Considerations
The economic advantages of modular solutions extend beyond initial capital expenditure considerations. While module fabrication may require higher upfront engineering costs, substantial savings are realized through reduced offshore construction hours, improved quality control, and shortened installation timeframes. The controlled environment of fabrication yards contributes to superior build quality and reduced rework requirements.
Process Module Solutions
Production Modules
Production modules form the core of offshore processing capabilities. These units typically incorporate primary separation, gas compression, and water treatment systems. Modern designs emphasize compact arrangements that optimize the weight-to-production ratio while maintaining accessibility for maintenance. Process modules increasingly incorporate smart instrumentation and control systems that enable remote monitoring and operation.
Gas Treatment Systems
Gas processing modules have evolved to address increasingly stringent export specifications and environmental regulations. These units incorporate membrane separation, molecular sieve dehydration, and amine sweetening systems. Modular design allows for future modification to accommodate changing gas compositions and processing requirements.
Water Treatment Facilities
Produced water treatment modules demonstrate the versatility of modular design principles. These systems integrate multiple treatment stages including hydrocyclones, flotation units, and membrane filtration systems. The modular approach enables staged implementation of water treatment capacity as production profiles evolve.
Utility Module Applications
Power Generation
Power generation modules have advanced significantly with the integration of combined cycle systems and waste heat recovery units. Modern designs incorporate dual-fuel capabilities and advanced emissions control systems. The modular approach facilitates maintenance through swap-out of major components and enables future upgrades to more efficient technologies.
Electrical Distribution
Electrical distribution modules serve as the power management centers for offshore facilities. These units house switchgear, transformers, and control systems in environmentally controlled spaces. Modular design enables factory testing of complete systems prior to offshore installation, significantly reducing commissioning time.
Chemical Injection Systems
Chemical management modules centralize the storage and distribution of production chemicals. These units incorporate sophisticated dosing systems and real-time monitoring capabilities. The modular approach enables modification of chemical treatment programs without significant facility modifications.
Living Quarters and Support Facilities
Accommodation Modules
Modern accommodation modules integrate advanced comfort and safety features while maximizing space utilization. These units incorporate noise reduction technologies, fire protection systems, and emergency escape provisions. Modular construction enables customization to specific operator requirements and regulatory standards.
Control Rooms and Technical Spaces
Integrated control room modules serve as the operational nerve centers of offshore facilities. These units incorporate advanced human-machine interfaces, communication systems, and emergency response capabilities. The modular approach enables factory integration and testing of complex control systems.
Construction and Integration Considerations
Fabrication Methodology
Module fabrication employs advanced construction techniques including automated welding, 3D printing of complex components, and sophisticated quality control systems. The use of standardized components and interfaces reduces manufacturing complexity while improving reliability. Factory acceptance testing includes comprehensive simulation of operating conditions.
Transportation Engineering
The transportation of modules requires sophisticated engineering analysis to ensure structural integrity during transit. Naval architects develop detailed motion response analyses and sea-fastening requirements. The modular approach enables optimization of transport vessel utilization through careful scheduling and layout planning.
Installation Considerations
Module installation procedures have evolved to minimize offshore construction activities. Advanced lifting technologies and self-installing modules reduce weather sensitivity and installation risks. Standardized connection systems accelerate the integration of modules into existing facilities.
Operational Considerations
Maintenance Strategy
Modular design facilitates maintenance through improved access and the potential for module replacement rather than in-situ repair. Maintenance programs incorporate condition monitoring systems that enable predictive maintenance strategies. The modular approach reduces production downtime during major maintenance activities.
Performance Optimization
Modern modules incorporate advanced control systems that enable real-time optimization of process performance. Digital twin technology allows operators to simulate process modifications before implementation. The modular approach enables incremental upgrades to maintain optimal performance throughout facility life.
Future Trends and Developments
Technology Integratio
The future of offshore modular solutions lies in increased integration of advanced technologies including artificial intelligence, autonomous systems, and advanced materials. Module designs increasingly incorporate provisions for future technology upgrades. Standardization efforts are driving increased interoperability between modules from different manufacturers.
Environmental Considerations
Environmental sustainability drives the development of new modular solutions including carbon capture systems, renewable energy integration, and zero-discharge water treatment systems. Module designs increasingly incorporate energy efficiency features and environmental monitoring capabilities.
Conclusion
Modular solutions continue to evolve as a cornerstone of offshore oil and gas development. The integration of advanced technologies, improved fabrication methods, and enhanced operational capabilities demonstrates the ongoing value of modular approaches. Future developments will further enhance the efficiency and sustainability of offshore operations through modular solutions.