Local Equipment Rooms (LERs) are dedicated, climate-controlled spaces within offshore platforms designed to house critical control, monitoring, and instrumentation equipment.
These specialized rooms serve as centralized control points for platform operations, containing:
- Distributed control systems (DCS)
- Programmable logic controllers (PLCs)
- Control panels
- Communication equipment
- Safety systems
- Data logging devices
Both driller cabins and Local Equipment Rooms are essential components of offshore drilling operations, designed to maximize efficiency, safety, and control in the challenging marine environment.
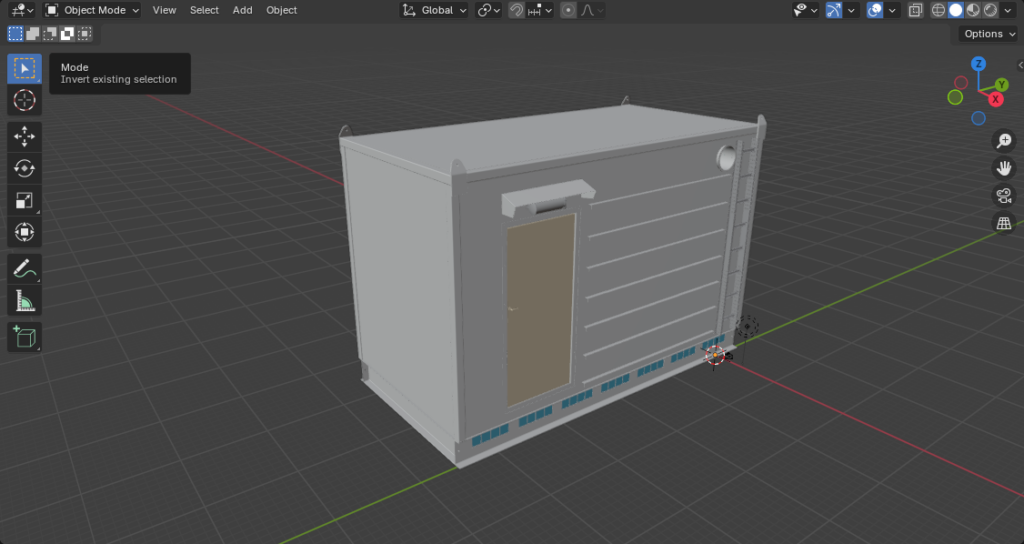
Key features include:
a) Ergonomic design to facilitate installation, maintenance, and repairs of electrical equipment and instrumentation
b) Robust construction: Designed to withstand harsh offshore conditions
c) Fire and blast resistance: Enhanced safety features to protect critical equipment
d) ATEX compliance: Located at or by the drill floor in classified areas due to presence of explosive atmosphere
e) Climate control and ventilation systems: Maintained for equipment preservation, proper air circulation to prevent overheating of machinery and ensure pressurization, where appropriate
f) Noise reduction: Insulation to minimize external noise for improved concentration
g) Electromagnetic interference protection

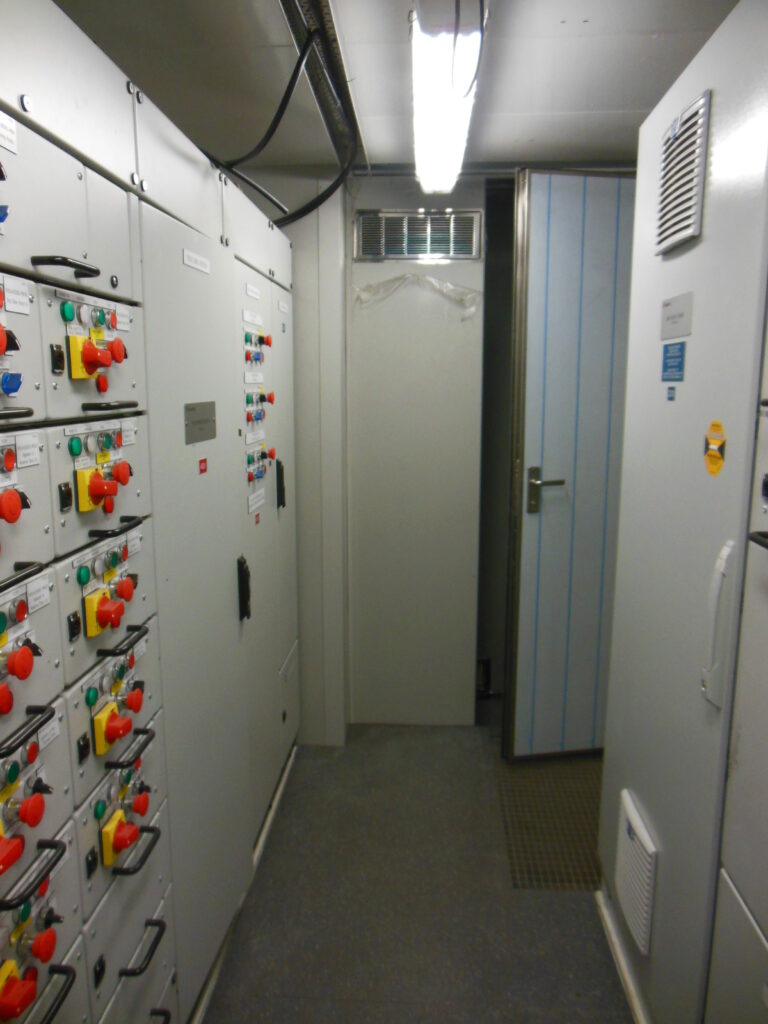
We can provide the following engineering services associated with the design and installation of driller cabins and local equipment rooms.
- Feasibility Study and Concept Design:
- Rig-specific analysis for system integration
- Evaluation of space availability and weight considerations
- Preliminary process flow diagrams
- Conceptual layout designs
- Initial cost estimates and project timeline
- Detailed Engineering Design:
- 3D modeling of the system layout
- Structural analysis for rig modifications
- Electrical system design and integration
- Insulation and fire rating
- Ventilation and pressurization
- ATEX classification and compliance
- Equipment Specification and Procurement Support:
- Development of technical specifications for major equipment
- Vendor evaluation and selection assistance
- Review of vendor documentation and drawings
- Structural Modifications Design:
- Design of new foundations or support structures for equipment
- Reinforcement designs for existing structures if required
- Finite Element Analysis (FEA) for critical structural components
- Integration Engineering:
- Interface design with existing rig systems
- Safety and Risk Engineering:
- Hazard and Operability (HAZOP) studies
- Failure Mode and Effects Analysis (FMEA)
- Safety Integrity Level (SIL) assessment
- Explosion risk assessment and zoning studies
- Regulatory Compliance and Classification:
- Liaison with classification societies
- Preparation of documentation for class approval
- Development of operational procedures to meet regulatory requirements
- Installation Planning:
- Development of detailed installation procedures
- Creation of work packages for shipyard or offshore installation
- Lift plans for major equipment
- Installation sequence optimization
- Commissioning and Start-up Support:
- Development of commissioning procedures
- Supervision of installation and commissioning activities
- Performance of system tests and trials
- Troubleshooting and optimization support
- Documentation and Training:
- Preparation of operating and maintenance manuals
- Development of crew training programs
- Environmental Impact Assessment:
- Support for environmental permit applications
- Project Management:
- Overall project scheduling and coordination
- Cost control and progress reporting
- Quality assurance and control
- Lifecycle Support:
- Development of maintenance and inspection schedules
- Optimization studies for long-term operation
- Technical support for system upgrades or modifications
- Feasibility Study and Concept Design:
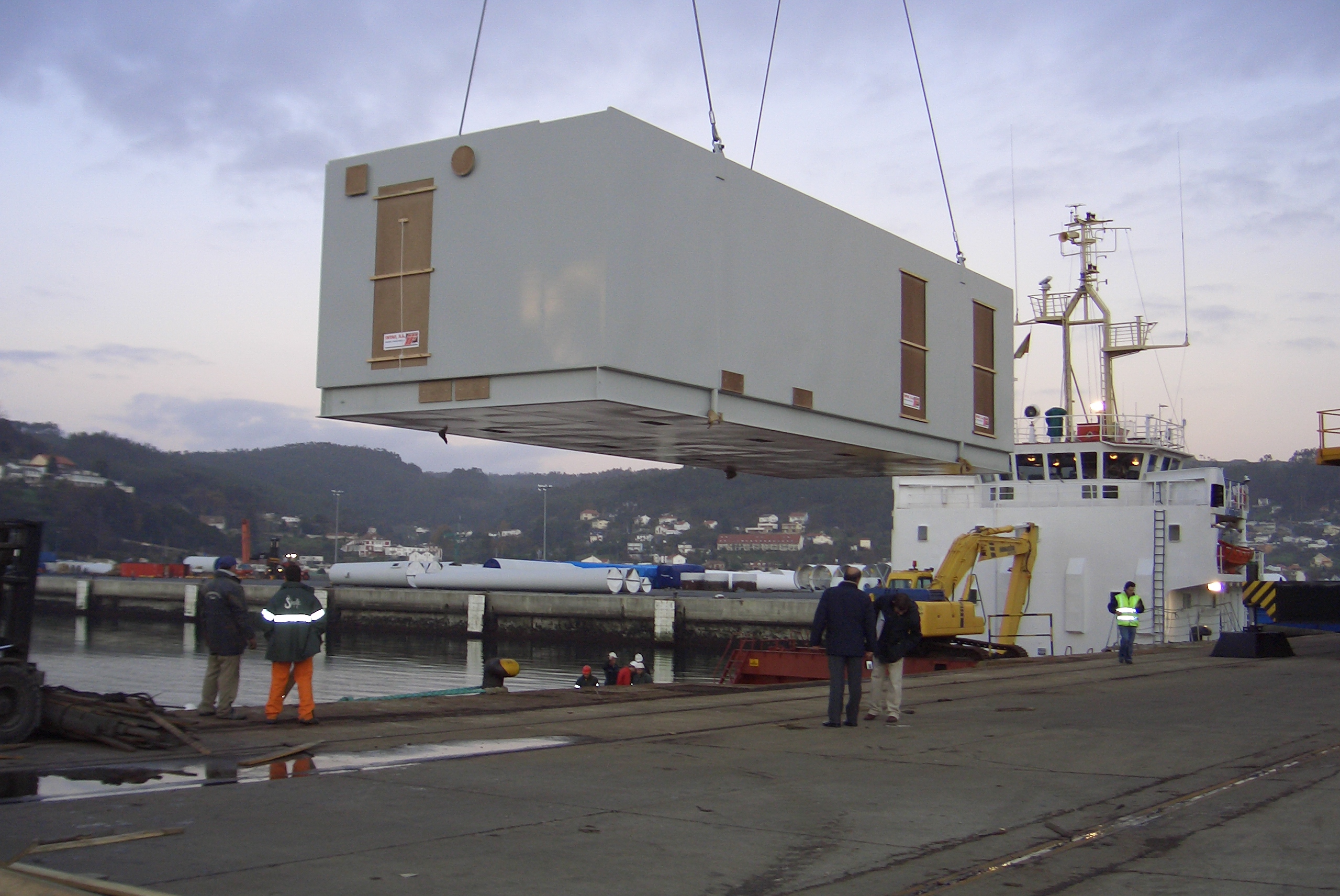
Please follow this link to download our brochure showcasing typical scopes of supply.