ISO freight containers, governed by the International Organization for Standardization under ISO 668 and related standards, are the most recognizable containers worldwide. These units are designed for seamless transportation across multiple modes—ship, rail, and truck—without the need for repacking. They come in standardized sizes, such as 20-foot and 40-foot variants, making them highly versatile for global shipping. The emphasis in their design is on modularity, stackability, and cost efficiency, ensuring that they can be used within the vast network of containerized shipping and logistics.
On the other hand, DNV offshore containers, built according to DNV-ST-E271 (formerly DNV 2.7-1), serve an entirely different purpose. While they share a similar function of cargo transport, their primary focus is on surviving extreme offshore conditions, withstanding harsh weather, and ensuring safe lifting operations under dynamic loads. Unlike ISO containers, which are optimized for stable environments and uniform handling procedures, DNV offshore containers are engineered for frequent lifting between supply vessels and offshore platforms, often under unpredictable sea states and heavy wind loads.
Structurally, the differences are immediately apparent. ISO freight containers are designed for high-volume, efficient transport and have a relatively lightweight steel frame with corrugated steel walls. Their corner castings allow for interlocking and stacking during transport, providing a uniform and modular approach to cargo movement. However, while robust for their intended purpose, these containers lack the reinforced structures necessary for offshore lifting. They rely on twist locks for securing and standard spreader bars for hoisting, which work well in controlled port environments but are unsuitable for the irregular lifting conditions found offshore.
DNV offshore containers, in contrast, feature heavier steel construction with reinforced frames, thicker plating, and impact-resistant design. They are built to endure significant mechanical stress, constant exposure to saltwater, and extreme temperature variations. The lifting mechanism is a key differentiator, as these containers are designed with certified padeyes for direct lifting via wire rope slings or chains, eliminating the need for spreader bars and allowing for more secure lifting operations. The four-point or multi-point sling arrangements prevent excessive movement during hoisting, reducing the risk of uncontrolled swinging, which can be hazardous in offshore operations.
Another fundamental distinction between the two container types is testing and certification. ISO freight containers undergo static load tests, stacking tests, and weather resistance assessments, ensuring they meet the required strength and durability for intermodal transport. However, their testing does not account for dynamic lifting, high-impact drops, or exposure to extreme marine conditions. In contrast, DNV offshore containers undergo a far more rigorous testing regime, including drop tests, load distribution tests, and lifting assessments under real-world offshore conditions. These tests simulate the intense forces encountered when containers are lifted from a moving supply vessel to a heaving offshore platform. This ensures that structural failures, weak points, or material fatigue are identified before deployment, significantly increasing operational safety.
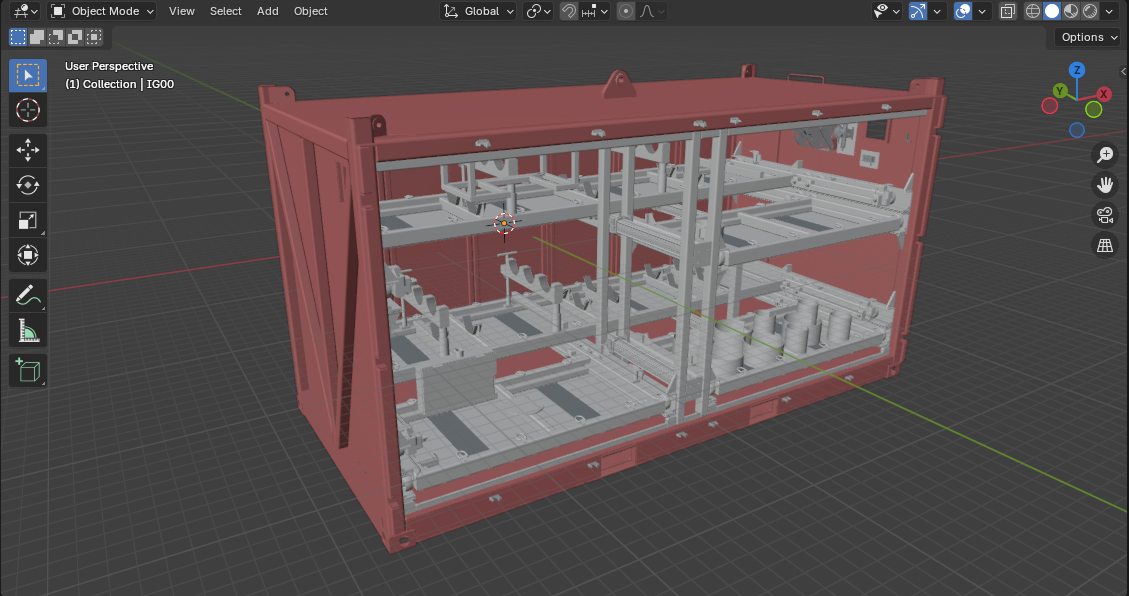
Beyond structural differences, environmental resistance also sets these two container types apart. While ISO containers are coated with marine-grade paint to resist rust and corrosion, their long-term durability in offshore conditions is limited. Continuous exposure to salt spray, high humidity, and extreme temperatures accelerates the degradation of standard ISO container materials, often leading to corrosion and reduced structural integrity over time. In contrast, DNV offshore containers are designed for prolonged offshore exposure, incorporating corrosion-resistant coatings, weatherproof seals, and reinforced door mechanisms that maintain their integrity even in the most extreme marine environments.
The intended use cases for each container type further highlight their distinctions. ISO freight containers are predominantly used for global shipping, warehouse storage, and inland transport, where controlled loading and unloading conditions prevail. They are an ideal choice for cost-effective, large-scale logistics operations where standardization and efficient handling take priority. However, when it comes to offshore operations, their lack of dynamic lifting capability, limited weather resistance, and reduced structural reinforcement make them unsuitable for direct offshore use without modification.
DNV offshore containers, by contrast, are specifically built for offshore energy projects, subsea operations, and oil and gas platforms. Their robust lifting capabilities, enhanced durability, and compliance with offshore safety standards make them essential for transporting tools, chemicals, equipment, and even personnel modules in hazardous offshore conditions. Whether used for mud skips, workshop units, or refrigerated storage for sensitive cargo, their superior design ensures that they can withstand the toughest offshore challenges while maintaining operational safety.
From an economic standpoint, ISO freight containers are significantly more affordable, as they are mass-produced and standardized for high-volume production. This makes them a practical solution for shipping companies and industries that require large-scale, cost-efficient cargo transport. However, their lower price point comes at the cost of reduced suitability for offshore environments, often necessitating additional modifications if they are to be used in marine energy projects.
DNV offshore containers, while more expensive due to their specialized design, certification, and safety requirements, provide a long-term investment in offshore safety and reliability. Their increased durability reduces the need for frequent replacements, and their compliance with offshore regulations ensures that they remain operationally viable without additional certification hurdles. For companies operating in high-risk offshore environments, the added cost is justified by the reduced risk of equipment failure, cargo loss, or accidents during lifting operations.
In summary, while ISO freight containers and DNV offshore containers may appear similar in form, their design philosophy, structural integrity, and operational requirements place them in entirely different categories. ISO containers are built for efficiency in a controlled, high-volume logistics environment, prioritizing standardization and cost-effectiveness. DNV offshore containers, however, are engineered for survivability in the most challenging offshore conditions, where unpredictable weather, dynamic lifting, and high-impact forces require a level of durability and safety that standard ISO containers simply cannot provide. For offshore engineers, logistics specialists, and project managers, choosing the correct container type is essential to ensuring compliance, safety, and operational efficiency in demanding offshore environments.