Selecting the right offshore container for the transportation and storage of hazardous goods is a critical task that demands meticulous attention to detail, a deep understanding of regulatory requirements, and a thorough assessment of the specific hazards associated with the cargo. Hazardous goods, which include flammable, toxic, corrosive, or reactive substances, pose significant risks to personnel, assets, and the environment if not handled properly. Offshore containers designed for hazardous goods must meet stringent safety standards and be tailored to the unique characteristics of the cargo.
Understanding the Nature of Hazardous Goods
The first step in selecting the right offshore container is to thoroughly understand the nature of the hazardous goods being transported or stored. Hazardous goods are classified based on their properties and the risks they pose. These classifications include flammable liquids and gases, toxic substances, corrosive materials, oxidizing agents, and reactive chemicals. Each category has specific handling and storage requirements that must be addressed by the container design.
For example, flammable liquids require containers with features such as flame arrestors, pressure relief valves, and grounding points to prevent ignition and control vapor release. Corrosive substances necessitate containers made from materials resistant to chemical attack, such as stainless steel or specially coated carbon steel. Toxic materials may require airtight seals and filtration systems to prevent leakage and protect personnel. Understanding the specific hazards associated with the goods is essential for selecting a container that can mitigate these risks effectively.
Compliance with International Standards and Regulations
Offshore containers for hazardous goods must comply with a range of international standards and regulations to ensure their safety and reliability. Key standards include those set by the International Maritime Organization (IMO), particularly the International Maritime Dangerous Goods (IMDG) Code, which provides guidelines for the safe transportation of hazardous materials by sea. The IMDG Code outlines specific requirements for container design, labeling, and documentation, ensuring that hazardous goods are handled safely throughout their journey.
Additionally, the International Organization for Standardization (ISO) has developed standards such as ISO 1496, which specifies the requirements for offshore containers, including those used for hazardous goods. These standards cover aspects such as structural integrity, lifting points, and safety features, ensuring that the containers can withstand the harsh offshore environment and the dynamic loads encountered during transportation and lifting operations.
Classification societies, such as Det Norske Veritas (DNV), the American Bureau of Shipping (ABS), and Lloyd’s Register, also play a crucial role in certifying offshore containers. These organizations conduct rigorous assessments of container designs, materials, and safety features to ensure compliance with international standards. Selecting a container that has been certified by a recognized classification society provides assurance that it meets the highest safety and quality standards.
Container Design and Safety Features
The design of an offshore container for hazardous goods must incorporate specific safety features to address the risks associated with the cargo. One of the primary considerations is the container’s structural integrity. The container must be constructed from high-strength, corrosion-resistant materials capable of withstanding the harsh offshore environment and the dynamic loads encountered during transportation and lifting operations. Reinforced corners, lifting points, and impact-resistant surfaces are essential to prevent structural failure and ensure safe handling.
Ventilation is another critical design feature for containers carrying hazardous goods. Proper ventilation helps to prevent the buildup of flammable or toxic vapors, reducing the risk of explosions or poisoning. Containers for flammable goods may be equipped with flame arrestors and pressure relief valves to control vapor release and prevent ignition. For toxic substances, airtight seals and filtration systems may be required to prevent leakage and protect personnel.
Containers for corrosive materials must be designed with chemical-resistant linings or coatings to prevent degradation and leakage. Additionally, these containers should have secure closures and secondary containment systems, such as spill trays or sumps, to capture any leaks or spills and prevent environmental contamination.
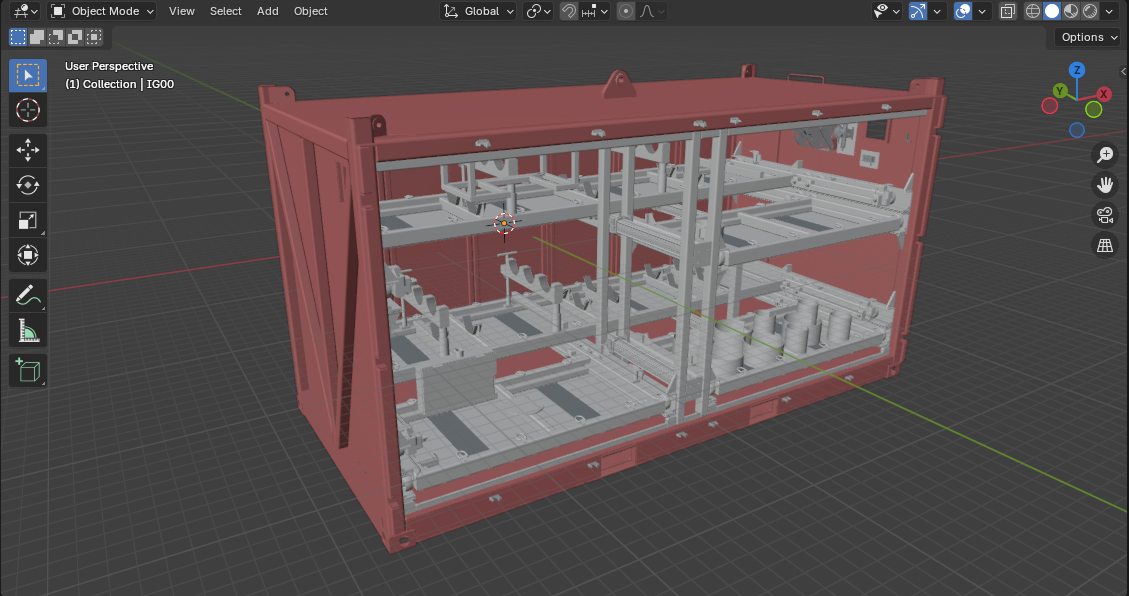
Environmental and Operational Considerations
Environmental considerations are paramount when selecting an offshore container for hazardous goods. The container must be designed to minimize the risk of environmental contamination in the event of a spill or leak. This includes features such as double-walled construction, spill containment systems, and corrosion-resistant materials. Additionally, the container should be equipped with labeling and placarding to clearly identify the hazardous nature of the contents, ensuring that personnel are aware of the risks and can take appropriate precautions.
Operational considerations also play a significant role in the selection process. The container must be compatible with the lifting and handling equipment used on the offshore installation, including cranes, helicopters, and supply vessels. Standardized lifting points and dimensions ensure that the container can be safely and efficiently transported and integrated with existing infrastructure. The container’s weight and size must also be considered to ensure that it can be handled within the operational limits of the offshore installation.
Risk Assessment and Mitigation
A thorough risk assessment is essential when selecting an offshore container for hazardous goods. This assessment should identify the potential hazards associated with the cargo and evaluate the risks of transportation, storage, and handling. The findings of the risk assessment should inform the selection of a container with appropriate safety features and design characteristics to mitigate these risks.
For example, if the risk assessment identifies a high potential for fire or explosion, the selected container should have advanced fire suppression systems, explosion-proof features, and robust structural integrity. If the primary concern is environmental contamination, the container should have secondary containment systems and be constructed from materials resistant to chemical attack.
Certification and Inspection
Certification and regular inspection are critical components of ensuring the safety and reliability of offshore containers for hazardous goods. The container must undergo a rigorous certification process, which includes design review, material testing, and on-site inspections by a recognized classification society. This process verifies that the container meets the required safety standards and is fit for purpose.
Regular inspections and maintenance are also necessary to ensure the ongoing safety and performance of the container. Inspections should be conducted by qualified personnel and include checks for structural damage, corrosion, and wear and tear. Any issues identified during inspections must be addressed promptly to maintain the container’s certification and ensure its safe use in offshore operations.
Conclusion
Selecting the right offshore container for hazardous goods is a complex and critical task that requires a thorough understanding of the cargo, compliance with international standards, and careful consideration of design, safety, and operational factors. By prioritizing safety, reliability, and environmental protection, operators can ensure the safe and efficient transportation and storage of hazardous goods in the challenging offshore environment. The selection process should be guided by a comprehensive risk assessment and informed by the expertise of classification societies and regulatory bodies. With the right container in place, operators can mitigate risks, protect personnel and assets, and ensure the successful execution of offshore operations involving hazardous goods.