Regular inspection is the first line of defense in offshore container maintenance. Offshore classification bodies such as DNV, Lloyd’s Register, and Bureau Veritas mandate periodic checks to ensure that containers remain structurally sound and safe for offshore lifting operations. These inspections typically occur every six to twelve months, depending on usage intensity and environmental exposure. Visual assessments focus on weld integrity, corrosion levels, padeye condition, and the functionality of doors and locking mechanisms. Advanced non-destructive testing (NDT) techniques, such as magnetic particle inspection (MPI) and ultrasonic testing (UT), are used to detect hidden cracks, material fatigue, and internal weaknesses that could compromise structural integrity. If any defects are found, immediate action must be taken to repair or reinforce the affected areas before the container is certified for further use.
Corrosion control is one of the most critical aspects of offshore container maintenance. Given the continuous exposure to salt-laden air and seawater, corrosion can weaken steel structures, compromise load-bearing capacity, and accelerate deterioration. Preventing corrosion begins with high-quality protective coatings, typically applied during the manufacturing process. However, over time, these coatings degrade due to mechanical wear, impact damage, and environmental factors. Regular repainting and touch-ups with marine-grade, anti-corrosive coatings are necessary to maintain a protective barrier. In cases where severe corrosion has penetrated the metal surface, abrasive blasting or chemical treatment may be required before applying new protective layers. Stainless steel components, where applicable, provide enhanced resistance to rust but still require regular maintenance to prevent pitting and surface contamination.
Structural damage, often caused by rough handling, repeated lifting, or accidental impact with other heavy equipment, requires immediate repair to maintain container integrity. The most common damage areas include padeyes, corner castings, base frames, and side panels. Padeyes, which bear the entire load during offshore lifting operations, must be closely monitored for cracks, deformations, or weld failures. Any defect in a lifting point presents a serious safety hazard, and damaged padeyes should be repaired or replaced following welding procedures that meet offshore certification standards. Similarly, any buckling or cracking in the structural frame demands reinforcement or re-welding by certified offshore welders using appropriate materials and techniques to restore strength without introducing heat-induced weaknesses.
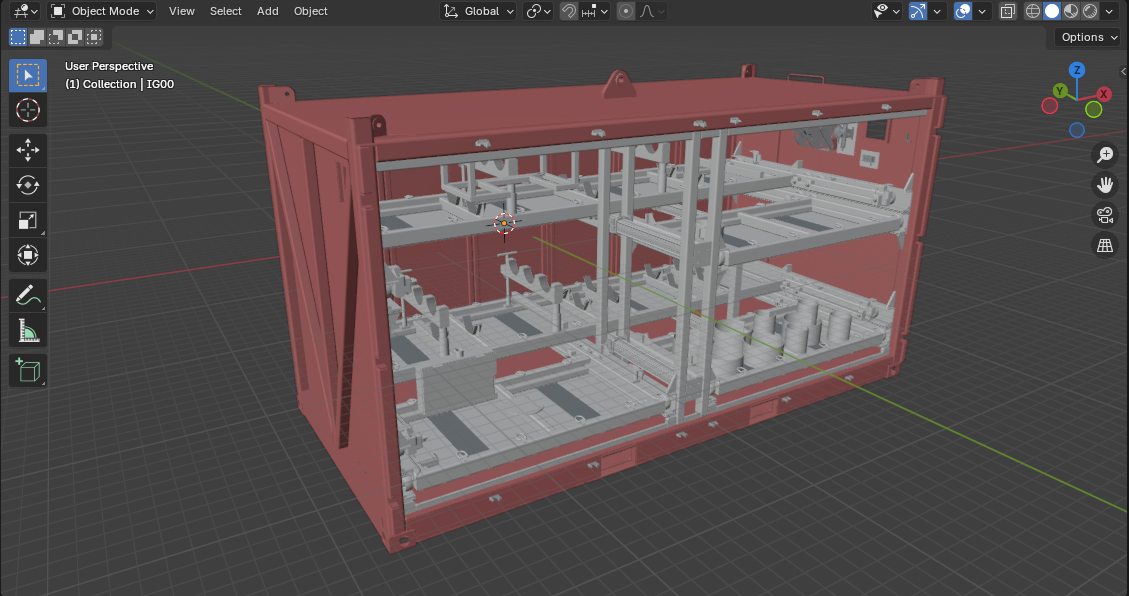
The functionality of doors, seals, and locking mechanisms is another key maintenance consideration. Offshore containers are frequently used for transporting sensitive equipment, hazardous materials, or weather-sensitive goods, making it essential that doors remain securely sealed against water ingress, dust, and extreme temperatures. Rubber seals around doors tend to degrade over time, becoming brittle or losing elasticity, leading to water leaks or difficulty in closing the container properly. Routine replacement of these seals ensures that internal cargo remains protected and offshore regulatory requirements for weatherproofing are met. Hinges and locking bars should be regularly lubricated and checked for misalignment, as corroded or seized components can impede access and compromise container security.
Beyond immediate maintenance tasks, weld integrity assessments and load-bearing tests play a crucial role in determining whether a container is fit for continued offshore service. Offshore containers are subject to significant dynamic loads during lifting and transport, and any fatigue-induced weaknesses in welds or structural elements can lead to failure under stress. Certified welding repairs must be carried out in accordance with DNV-ST-E271, ISO 10855, or equivalent offshore standards, using materials that match the original structural strength. Following major repairs, load tests are conducted to verify that the container can safely handle its rated capacity without deformation or failure. These tests are often required for re-certification, ensuring compliance with offshore regulations before the container is returned to service.
Maintaining offshore containers also involves proper handling and storage procedures. When not in use, containers should be stored in designated areas with adequate ventilation and minimal exposure to standing water or chemical contaminants. Stacking should be done carefully to avoid unnecessary stress on corner castings and base frames, reducing the likelihood of deformation. Improper stacking or overloading during storage can lead to structural fatigue, alignment issues, and increased wear on load-bearing components. Proper handling during transport, including the use of certified lifting slings and adherence to correct lifting angles, further extends the lifespan of offshore containers by minimizing unnecessary mechanical stresses.
Repairs must always be documented and carried out in accordance with offshore certification standards. Offshore regulatory bodies require that all maintenance, repairs, and modifications be logged for audit purposes, ensuring traceability and compliance. Containers that undergo major structural repairs often need re-certification by an accredited inspection authority, validating that the restoration work meets offshore operational requirements. Failure to maintain proper records can lead to compliance issues and potential decommissioning of the container from offshore service.
Over time, despite the best maintenance practices, offshore containers will reach the end of their operational lifespan due to cumulative wear, corrosion, and regulatory changes. Containers that are beyond economical repair may be decommissioned, scrapped, or repurposed for non-critical applications, such as onshore storage units or modified workspaces. However, proactive maintenance significantly delays the need for replacement, maximizing return on investment while ensuring continued operational safety.
Maintaining and repairing offshore containers is not just about prolonging their usable life; it is a critical aspect of offshore safety, regulatory compliance, and operational efficiency. Through regular inspections, corrosion control, structural repairs, and proper handling, offshore containers can remain fully functional and safe for years, even in the most challenging marine environments. Investing in a robust maintenance program minimizes the risk of unexpected failures, reduces downtime, and ensures that offshore operations can proceed without costly interruptions or safety concerns.