Industrial filtration systems play a critical role in process engineering, particularly in water treatment and waste processing.
Basket Strainers
Basket strainers serve as robust preliminary filtration devices, typically handling large-volume fluid streams where coarse particle removal is essential. These units consist of a cylindrical perforated basket housed within a pressure vessel, with mesh sizes of different sizes. The key advantage of basket strainers lies in their serviceability – the removable basket design allows for quick cleaning and minimal process downtime. However, they require regular maintenance to prevent pressure drop across the system and potential breakthrough of collected solids.
To simplify the maintenance requirements, basket strainers can be designed with automatic self cleaning features which minimize downtime and maintenance effort.
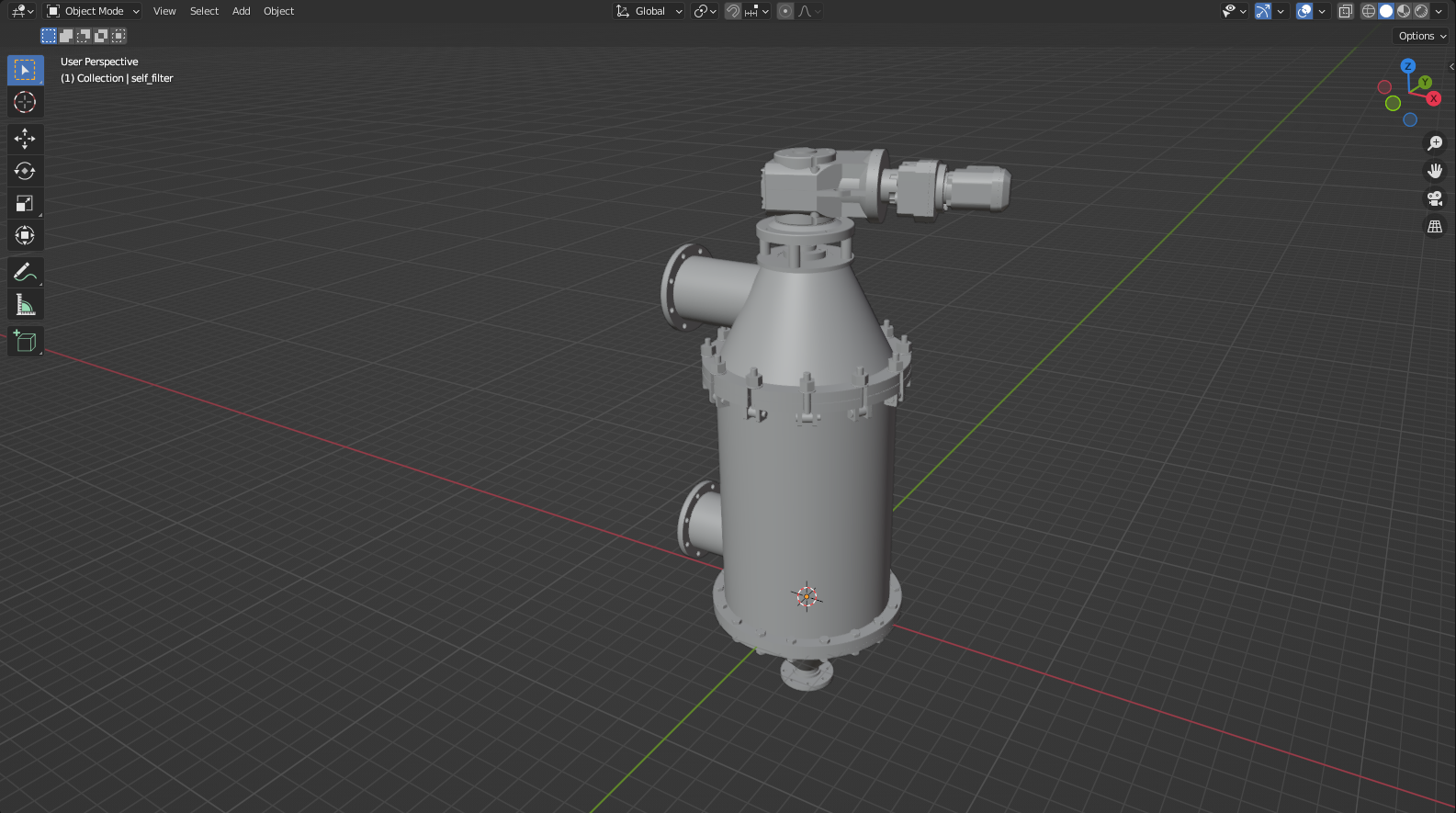
Current industrial designs incorporate features such as differential pressure indicators and quick-release covers, enabling operational optimization. The pressure vessel typically operates at working pressures up to 150 psig, with specialized units available for higher-pressure applications. Material selection usually favors stainless steel construction for corrosion resistance, though carbon steel options exist for less demanding applications.
Screw Presses
Screw presses represent a relatively sophisticated approach to dewatering, particularly effective in sludge processing applications. The core mechanism consists of a helical screw operating within a cylindrical screen housing. As the screw rotates, it simultaneously conveys and compresses the material, forcing water through the screen while retaining solids.
Modern screw press designs achieve dewatering efficiencies of 20-30% dry solids content, depending on feed characteristics. Key design parameters include:
- Screw pitch progression: typically decreasing along the length to enhance compression
- Screen aperture size: commonly 0.25-1.0mm, selected based on particle size distribution
- Operating speed: usually 1-5 rpm to optimize retention time and compression
Performance optimization in screw press operations depends heavily on feed consistency and polymer conditioning. Recent developments include variable-frequency drives for speed control and automated backwash systems to maintain screen cleanliness.
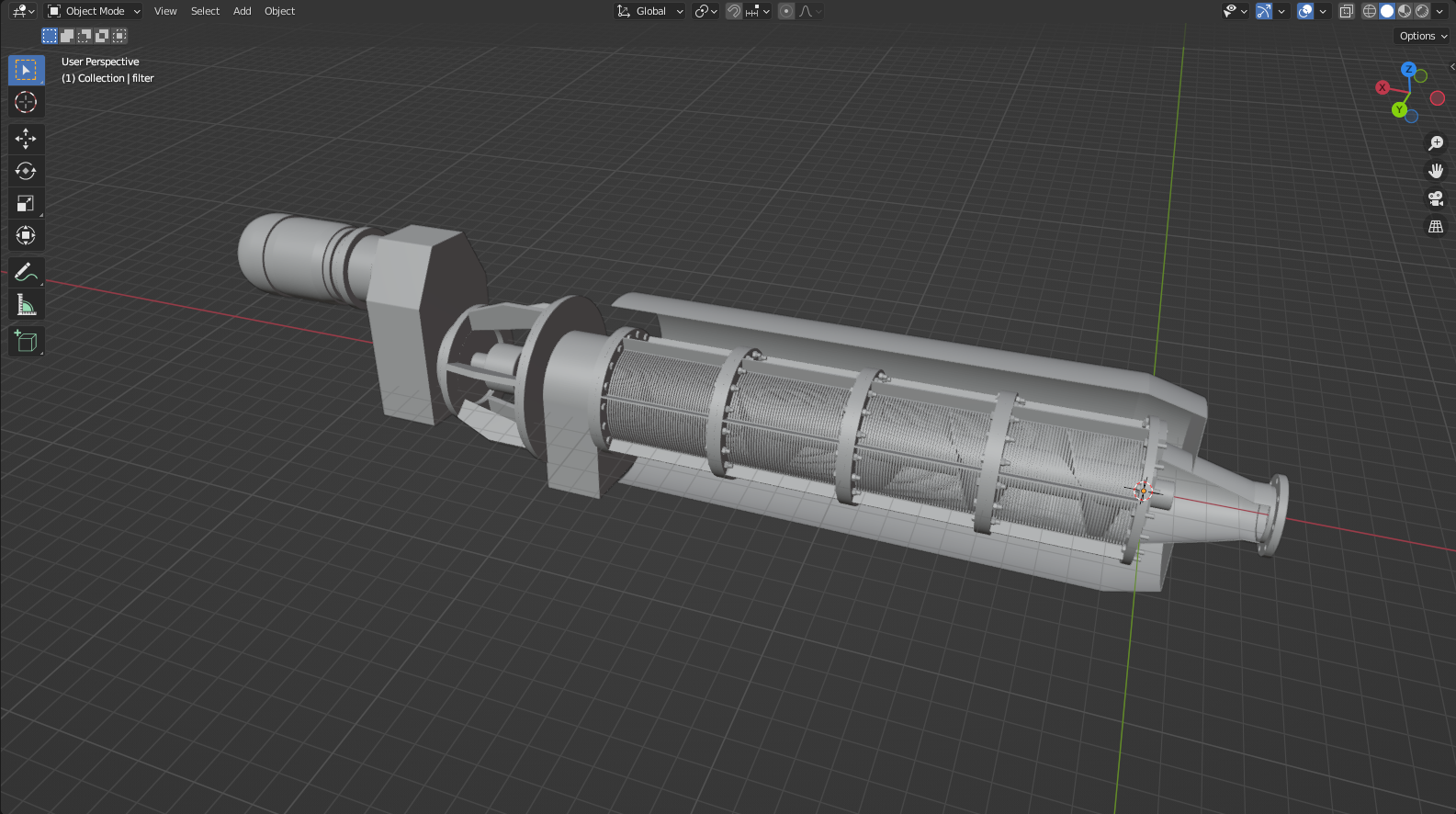
The mechanical reliability of these systems, coupled with their continuous operation capability, makes them particularly valuable in municipal and industrial wastewater treatment applications. Energy consumption typically ranges from 0.5-2.0 kWh per cubic meter of sludge processed, representing a relatively efficient dewatering solution compared to centrifugal alternatives.
Cyclone Separators
Drill cuttings cyclone separators are key components in the solids control and waste management system on offshore drilling rigs. Their primary function is to separate dust from the cuttings-air two phase flow. The main highlights of this equipment are as follows:
- Conical shape with a cylindrical top section
- No moving parts, which reduces maintenance requirements
- Typically made of wear-resistant materials
- Uses centrifugal force to separate particles based on their size and density
- The mixture enters tangentially at high velocity, creating a rotating vortex
- Heavier particles (cuttings) are forced to the outer walls and spiral downward
- Lighter particles and air phase move to the center and are drawn upward
- Efficiency depends on factors like flow rate, pressure, and fluid properties
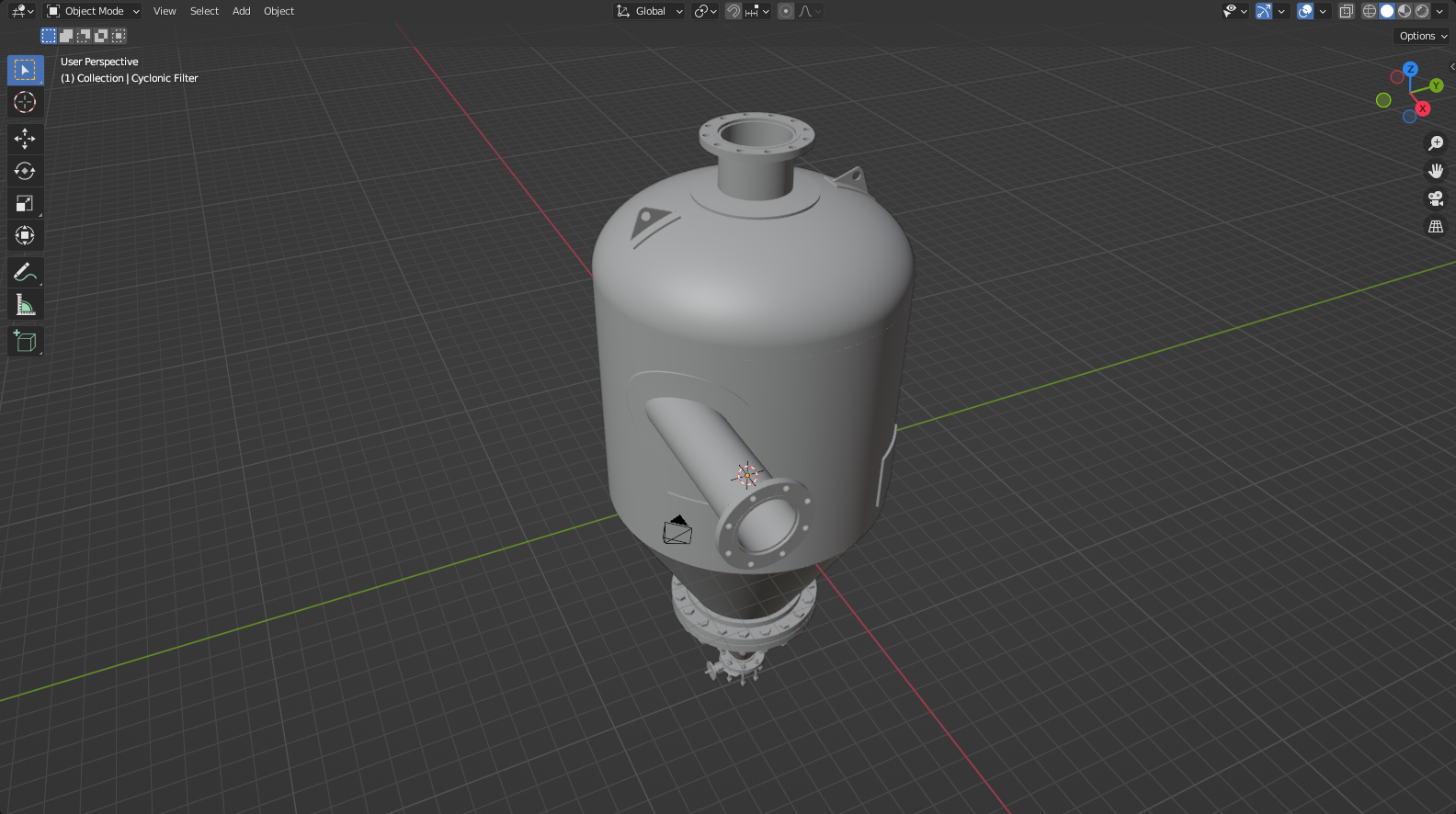
Rock catchers
A rock catcher is a critical component of the solids control equipment in a drilling fluid system, typically installed in the surface flow line between the wellhead and the shale shakers. Its primary purpose is to prevent large cuttings and debris from reaching and potentially damaging downstream equipment.
When drilling fluid enters the rock catcher, the flow velocity decreases due to the larger cross-sectional area. This velocity reduction allows heavier particles to settle into the basket while the drilling fluid continues through the perforations. The caught material can then be periodically removed during basket cleaning operations. Regular maintenance is indeed crucial – the basket needs to be checked and emptied regularly to prevent overflow or bypass of large cuttings. A full or blocked rock catcher can lead to increased pressure in the flow line and potential equipment damage.
Broadly speaking, the most significant highlights of this type of bespoke design are as follows:
A) Main design features:
- A perforated basket or screen with relatively large openings
- A hinged or removable lid for easy access during cleaning
- A bypass system for maintenance operations
- Robust construction to handle high flow rates and abrasive materials
- Often equipped with a drain valve for emptying
B) Operational benefits:
- Protects expensive downstream equipment (especially shale shakers) from damage
- Prevents plugging of flow lines and equipment
- Allows for collection and analysis of large cuttings for geological evaluation
- Reduces maintenance requirements on subsequent solids control equipment