A drilling mud treatment system, also known as a drilling fluid system, is designed to circulate drilling fluid (mud) through the wellbore during drilling operations. The system serves multiple critical functions, including cooling and lubricating the drill bit, removing drill cuttings from the wellbore, controlling formation pressures, and maintaining wellbore stability.
To most basic process involving drilling fluid handling can be broken down as follows: drilling mud is pumped from the suction tank by the mud pumps, and it is sent down the drill string, exiting through nozzles in the drill bit. The drilling mud then carries back drill cuttings up the annulus between the drill string and wellbore. Back at the surface, the drilling mud flows over the shale shakers, where large cuttings are removed. The mud then passes through finer solids removal equipment (desander, desilter, centrifuges) and degassing equipment, which removes any entrained gases. The cleaned mud returns to the suction tank to be recirculated.
The process can be broken down as follows:
a) Mud Tanks (Pits): Required to store and condition the drilling fluid, typically involving multiple interconnected tanks with separate compartments for mixing, settling, and suction.
b)
Mud Pumps: Required to circulate the mud through the system, normally in low pressure for local circulation and high pressure (reciprocating piston pumps with high-volume capacity) to circulate the drilling mud down the well.
c) Mud Mixing Equipment: Required to mix and condition the drilling fluid, typically including hoppers, agitators, and chemical additives.
d) Shale Shakers: Required for solids removal, with vibrating screens that separate drill cuttings from the drilling mud which can be reused.
e) Desander and Desilter: Required to remove smaller particles missed by shale shakers.
f) Mud-Gas Separator: Required to separate entrained gas from the drilling mud, essential for for well control and safety.
g) Degasser: Required to remove dissolved gases from the drilling mud, maintaining adequate mud properties.
h) Centrifuges: Required to remove fine solids and recover barite, used for weight control and fluid maintenance.
i) Mud Coolers: Required for mud temperature control, typically used in deep, high-temperature Wells.
j) Mud Logger: Required to monitor and analyze mud properties and formation cuttings, providing real-time data on drilling progress and formation evaluation.
k) Bulk Storage Systems: Required to store dry additives (barite, bentonite, etc.), comprising silos and pneumatic transfer systems.
l) Chemical Mixing Systems: Required to add and mix liquid additives, comprising chemical tanks, pumps, and metering devices.
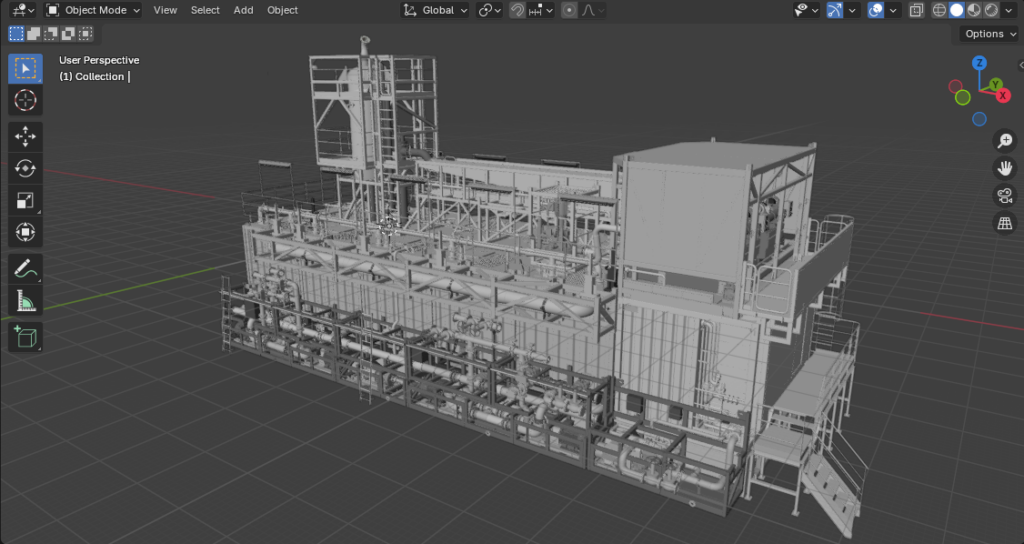
We can provide the following engineering services associated with the design and installation of a modular drilling mud treatment system.
- Feasibility Study and Concept Design:
- Rig-specific analysis for system integration
- Evaluation of space availability and weight considerations
- Preliminary process flow diagrams
- Conceptual layout designs
- Initial cost estimates and project timeline
- Detailed Engineering Design:
- Process engineering and equipment sizing
- Piping and Instrumentation Diagrams (P&IDs)
- 3D modeling of the system layout
- Structural analysis for rig modifications
- Electrical system design and integration
- Equipment Specification and Procurement Support:
- Development of technical specifications for major equipment
- Vendor evaluation and selection assistance
- Review of vendor documentation and drawings
- Structural Modifications Design:
- Design of new foundations or support structures for equipment
- Reinforcement designs for existing structures if required
- Finite Element Analysis (FEA) for critical structural components
- Integration Engineering:
- Interface design with existing rig systems
- Modification of existing piping systems
- Safety and Risk Engineering:
- Hazard and Operability (HAZOP) studies
- Failure Mode and Effects Analysis (FMEA)
- Safety Integrity Level (SIL) assessment
- Explosion risk assessment and zoning studies
- Regulatory Compliance and Classification:
- Liaison with classification societies
- Preparation of documentation for class approval
- Development of operational procedures to meet regulatory requirements
- Installation Planning:
- Development of detailed installation procedures
- Creation of work packages for shipyard or offshore installation
- Lift plans for major equipment
- Installation sequence optimization
- Commissioning and Start-up Support:
- Development of commissioning procedures
- Supervision of installation and commissioning activities
- Performance of system tests and trials
- Troubleshooting and optimization support
- Documentation and Training:
- Preparation of operating and maintenance manuals
- Development of crew training programs
- Environmental Impact Assessment:
- Support for environmental permit applications
- Project Management:
- Overall project scheduling and coordination
- Cost control and progress reporting
- Quality assurance and control
- Lifecycle Support:
- Development of maintenance and inspection schedules
- Optimization studies for long-term operation
- Technical support for system upgrades or modifications
- Feasibility Study and Concept Design:
These engineering services cover the entire spectrum of implementing a drilling fluid system on a drilling rig, from initial concept to installation and ongoing support. The goal is to ensure a safe, efficient, and compliant integration of the drilling fluid system into the rig’s existing operations.
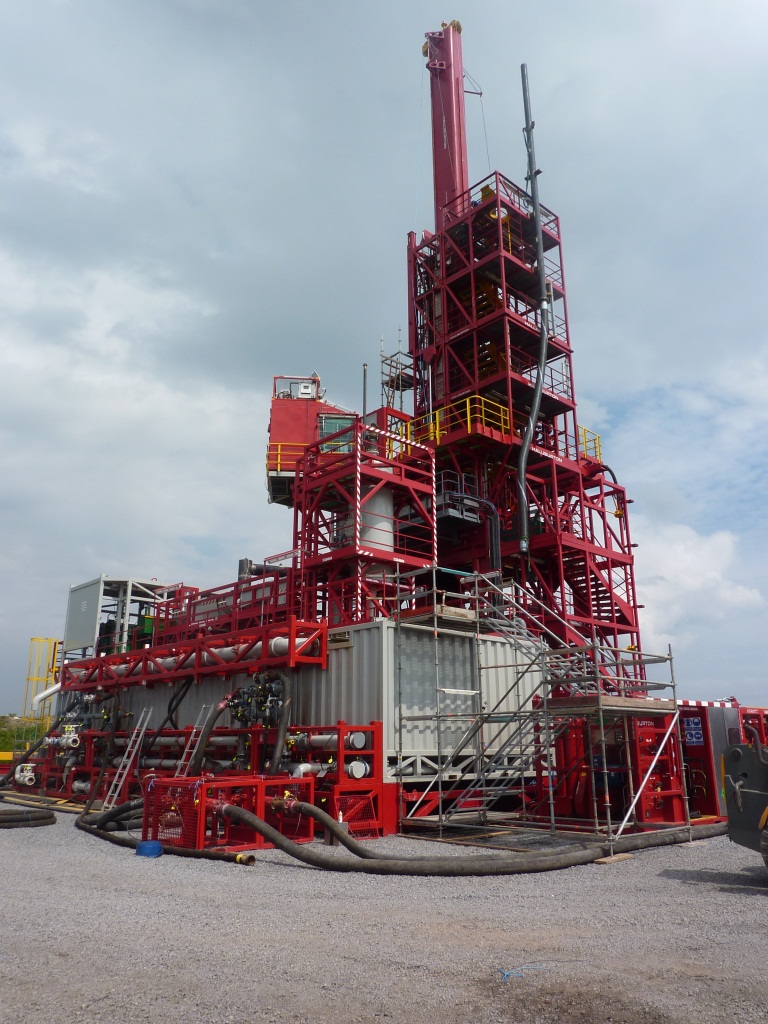
Please follow this link to download our brochure showcasing typical scopes of supply.