A drilling mud cooling system or mud cooler is a critical piece of equipment in offshore drilling operations, designed to maintain optimal temperature of the drilling fluid (mud) circulating through the wellbore.
The drilling mud cooling system plays a crucial role in maintaining the efficiency, safety, and cost-effectiveness of offshore drilling operations by precisely controlling the temperature of the drilling fluid.
Broadly speaking, the most significant highlights of this type of cooling system are as follows:
A) Functionality:
- Heat Removal and Mud Property Preservation: Extracts excess heat generated by friction in the wellbore and surface equipment. Maintains mud temperature within an optimal range (typically 50-60°C). Prevents degradation of mud properties due to overheating.
- Improved Drilling Efficiency: Optimizes mud properties for better drilling performance.
- Extended Equipment Life: Reduces thermal stress on drilling equipment.
- Enhanced Safety: Minimizes risks associated with overheated mud.
- Cost Reduction: Lowers mud replacement and treatment costs.
- Equipment Protection: Safeguards downhole tools and surface equipment from thermal damage.
- Wellbore Stability: Helps maintain wellbore stability by controlling mud temperature.
- Designed for seamless integration with existing mud circulation systems.
- Includes standardized connections for easy installation and replacement.
- May feature remote monitoring capabilities for integration with rig control systems.
- Engineered for space efficiency to minimize footprint on offshore platforms.
- May be vertically oriented to save deck space.
- Seawater: Readily available and cost-effective, but can lead to increased corrosion and fouling.
- Closed-loop glycol: Offers better temperature control and reduces corrosion issues, but requires additional equipment.
- Self-cleaning mechanisms (e.g., reversible flow or backwash)
- Chemical injection points for anti-fouling treatments
- Easy-access designs for manual cleaning during maintenance
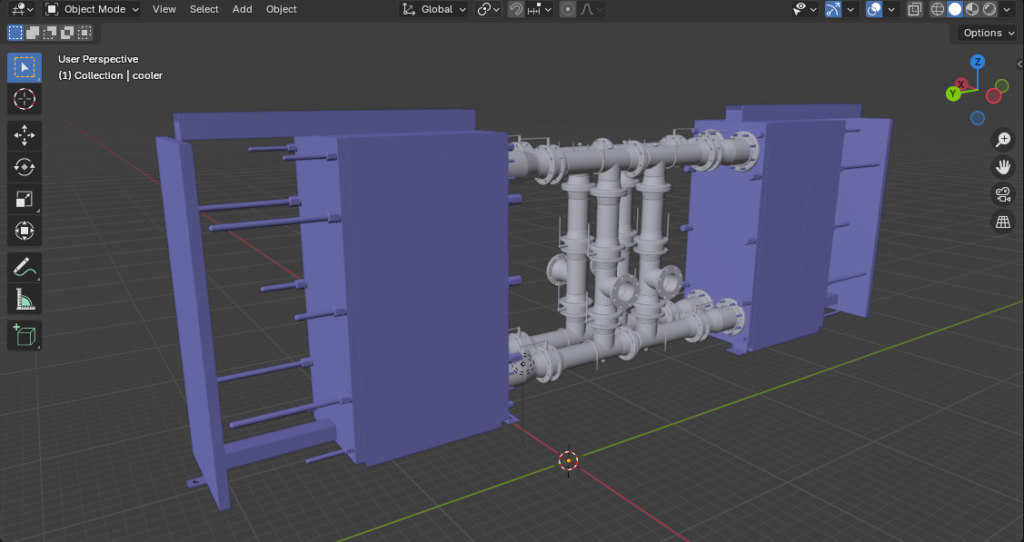
We can provide the following engineering services associated with the design and installation of a modular drilling mud cooling system.
- Feasibility Study and Concept Design:
- Rig-specific analysis for system integration
- Evaluation of space availability and weight considerations
- Preliminary process flow diagrams
- Conceptual layout designs
- Initial cost estimates and project timeline
- Detailed Engineering Design:
- Process engineering and equipment sizing
- Piping and Instrumentation Diagrams (P&IDs)
- 3D modeling of the system layout
- Structural analysis for rig modifications
- Electrical system design and integration
- Equipment Specification and Procurement Support:
- Development of technical specifications for major equipment
- Vendor evaluation and selection assistance
- Review of vendor documentation and drawings
- Structural Modifications Design:
- Design of new foundations or support structures for equipment
- Reinforcement designs for existing structures if required
- Finite Element Analysis (FEA) for critical structural components
- Integration Engineering:
- Interface design with existing rig systems
- Modification of existing piping systems
- Safety and Risk Engineering:
- Hazard and Operability (HAZOP) studies
- Failure Mode and Effects Analysis (FMEA)
- Safety Integrity Level (SIL) assessment
- Explosion risk assessment and zoning studies
- Regulatory Compliance and Classification:
- Liaison with classification societies
- Preparation of documentation for class approval
- Development of operational procedures to meet regulatory requirements
- Installation Planning:
- Development of detailed installation procedures
- Creation of work packages for shipyard or offshore installation
- Lift plans for major equipment
- Installation sequence optimization
- Commissioning and Start-up Support:
- Development of commissioning procedures
- Supervision of installation and commissioning activities
- Performance of system tests and trials
- Troubleshooting and optimization support
- Documentation and Training:
- Preparation of operating and maintenance manuals
- Development of crew training programs
- Environmental Impact Assessment:
- Support for environmental permit applications
- Project Management:
- Overall project scheduling and coordination
- Cost control and progress reporting
- Quality assurance and control
- Lifecycle Support:
- Development of maintenance and inspection schedules
- Optimization studies for long-term operation
- Technical support for system upgrades or modifications
- Feasibility Study and Concept Design:
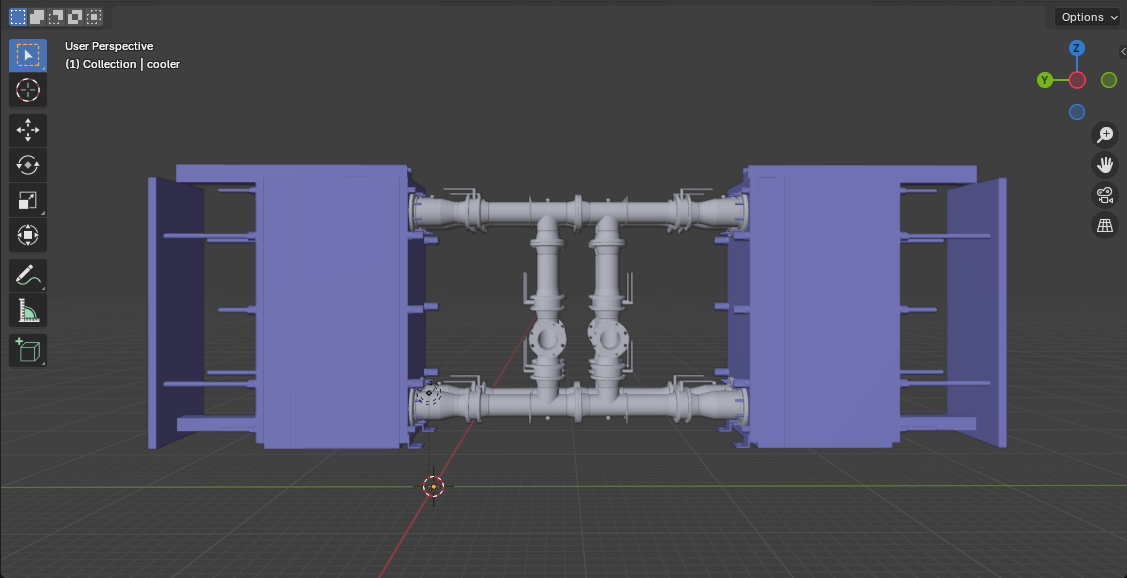
Please follow this link to download our brochure showcasing typical scopes of supply.