Offshore module fabrication and installation represent a significant portion of the overall cost of offshore projects, whether for oil and gas, wind, or other marine energy developments. Therefore, optimizing these processes for cost-effectiveness is crucial. This report explores key methods and solutions, focusing on strategies that balance cost reduction with safety and quality.
One of the primary drivers of cost in module fabrication is the location of construction. Onshore fabrication yards, particularly those with deep-water access, offer significant advantages. These yards allow for larger, more complex modules to be constructed in a controlled environment, minimizing weather delays and improving productivity. Furthermore, onshore fabrication typically benefits from readily available infrastructure, skilled labor pools, and easier access for material delivery, all contributing to lower overheads compared to offshore construction. However, the costs associated with transporting these large modules to the offshore site, including heavy lift vessels and specialized seafastening arrangements, must be carefully considered. The optimal choice between onshore and offshore fabrication depends heavily on the module size, complexity, and the distance to the installation location. For smaller, simpler modules, or projects in remote locations, some degree of offshore fabrication or assembly might still be economically viable.
Modular design itself is a powerful cost-saving tool. By breaking down the overall topside structure into smaller, manageable modules, fabrication can occur concurrently in multiple locations, shortening the overall project schedule. This parallelization not only reduces project duration but also allows for specialization, with different fabrication yards focusing on specific module types. Moreover, modular design simplifies integration and hook-up activities offshore. Well-defined interfaces between modules minimize the amount of on-site welding and testing, which are significantly more expensive and time-consuming in the offshore environment. This “plug-and-play” approach drastically reduces offshore man-hours and vessel time, leading to significant cost savings.
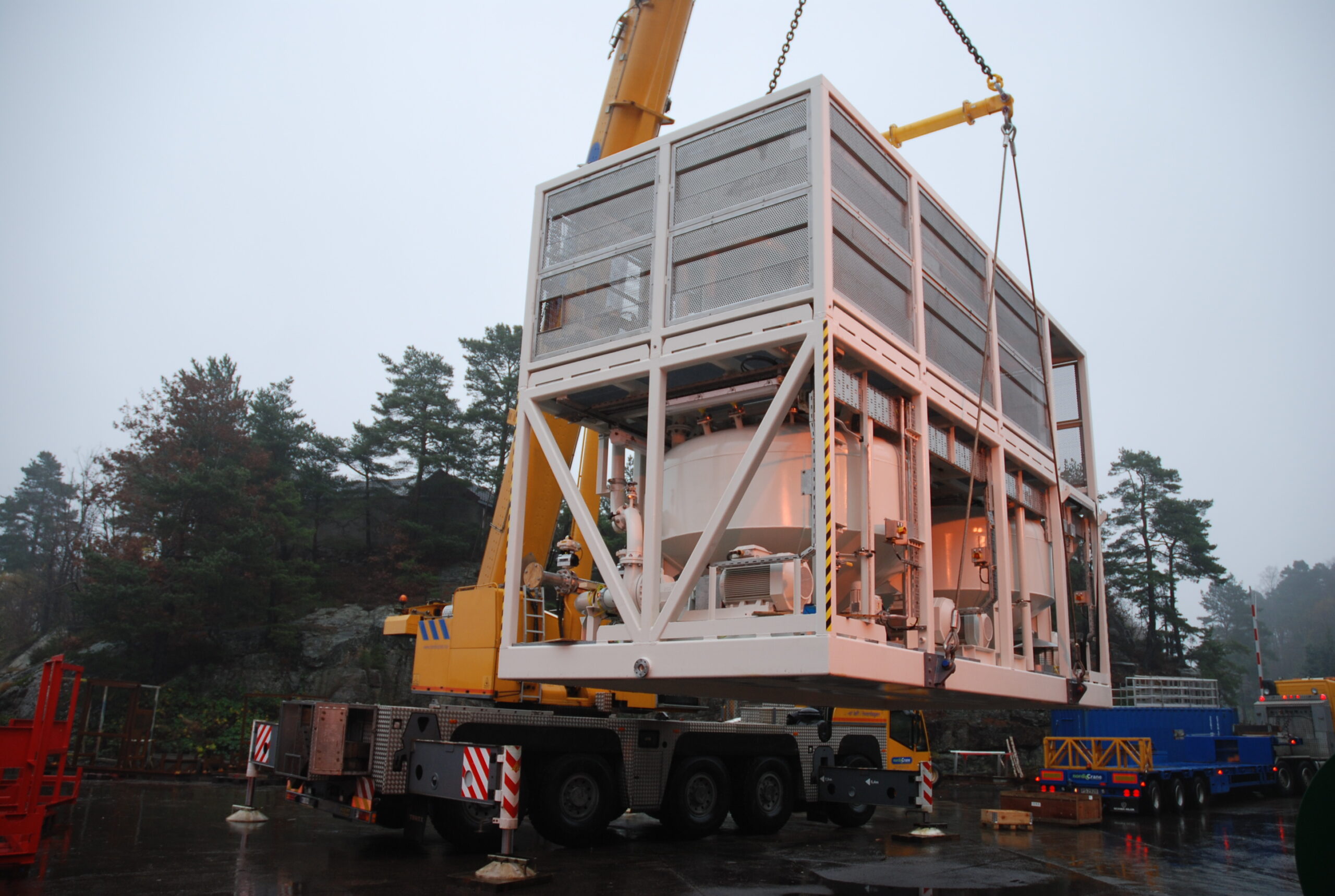
Installation methods also play a critical role in cost optimization. Heavy lift vessels (HLVs) are commonly employed for installing large modules. While HLVs provide the necessary lifting capacity, their day rates are substantial. Therefore, efficient planning and execution of lifting operations are essential. Minimizing the time required for mobilization, lifting, and demobilization of the HLV is paramount. This includes detailed lift studies, precise weather forecasting, and well-coordinated offshore operations. Alternative installation methods, such as float-over installation, can be considered for specific module types and water depths. Float-over involves ballasting a barge carrying the module into position over the substructure and then de-ballasting the barge to lower the module onto its foundations. This method can be more cost-effective than using an HLV, particularly for large, relatively shallow-draft modules.
Another area for cost reduction lies in the selection of materials and construction techniques. Utilizing high-strength steel or composite materials can reduce the weight of modules, leading to lower fabrication and installation costs. Advanced welding techniques, such as friction stir welding, can improve weld quality and reduce the time required for welding operations. Furthermore, employing automated fabrication processes, where feasible, can enhance productivity and reduce labor costs. However, any change in materials or construction techniques must be rigorously assessed to ensure compliance with relevant codes and standards and to maintain the required level of safety and reliability.
Finally, effective project management is essential for controlling costs throughout the module fabrication and installation process. This includes detailed cost estimation, rigorous change management procedures, and proactive risk management. Early engagement with key stakeholders, including fabricators, installation contractors, and certifying authorities, is crucial for identifying potential cost overruns and developing mitigation strategies. Utilizing digital tools, such as Building Information Modeling (BIM), can improve communication and coordination among project teams, leading to more efficient project execution. A well-defined project execution plan, coupled with effective communication and collaboration, is the cornerstone of any successful and cost-effective offshore module fabrication and installation project.