Drill cuttings reinjection (DCRI) has become a preferred waste management solution in the offshore oil and gas industry due to its environmental benefits and regulatory compliance. However, the implementation of DCRI systems can be capital-intensive, requiring significant investment in equipment, infrastructure, and operational expertise. For operators seeking to balance environmental responsibility with cost efficiency, adopting cost-effective DCRI solutions is essential.
Understanding the Cost Drivers of DCRI
To develop cost-effective DCRI solutions, it is important to first understand the primary cost drivers associated with the process. These include the capital expenditure (CapEx) for equipment such as slurrification units, injection pumps, and monitoring systems, as well as the operational expenditure (OpEx) for maintenance, energy consumption, and personnel. Additionally, the cost of drilling and completing injection wells, along with the expenses related to regulatory compliance and environmental monitoring, can significantly impact the overall budget.
By identifying these cost drivers, operators can focus on optimizing specific aspects of the DCRI process to achieve cost savings without compromising performance or environmental safety. The following sections outline key strategies for reducing costs while maintaining the effectiveness of DCRI systems.
Optimizing Injection Well Design and Location
One of the most significant costs in a DCRI system is the drilling and completion of injection wells. Optimizing the design and location of these wells can lead to substantial cost savings. For instance, selecting a suitable geological formation with high porosity and permeability can reduce the pressure required for injection, thereby lowering energy consumption and wear on equipment. Additionally, locating the injection well close to the drilling rig can minimize the need for extensive slurry transportation infrastructure, reducing both capital and operational costs.
Advanced geological and geophysical surveys can help identify optimal injection sites, ensuring that the selected formation can accommodate the volume of cuttings without risking fracture or contamination of surrounding formations. By investing in thorough site characterization upfront, operators can avoid costly issues such as well failures or regulatory penalties down the line.
Leveraging Modular and Scalable Equipment
The use of modular and scalable equipment is another effective strategy for reducing the costs of DCRI systems. Modular systems allow for incremental investment, enabling operators to start with a basic setup and expand as needed. This approach is particularly beneficial for smaller operators or those with limited initial budgets. Modular equipment can also be easily relocated and repurposed for different projects, maximizing its utility and reducing the need for redundant investments.
Scalable systems, on the other hand, allow for adjustments in capacity based on the volume of cuttings generated. This flexibility ensures that operators are not over-investing in equipment that exceeds their needs. For example, a scalable slurrification unit can be adjusted to handle varying volumes of cuttings, optimizing energy consumption and reducing operational costs.
Implementing Energy-Efficient Technologies
Energy consumption is a major operational cost in DCRI systems, particularly for high-pressure injection pumps. Implementing energy-efficient technologies can significantly reduce these costs. Variable frequency drives (VFDs) can be used to control the speed of injection pumps, ensuring that they operate at optimal efficiency based on the required injection pressure and flow rate. This not only reduces energy consumption but also extends the lifespan of the equipment by minimizing wear and tear.
Additionally, the use of renewable energy sources, such as solar or wind power, can further reduce energy costs, particularly in remote offshore locations where access to grid power is limited. While the initial investment in renewable energy infrastructure may be high, the long-term savings and environmental benefits can outweigh the costs.
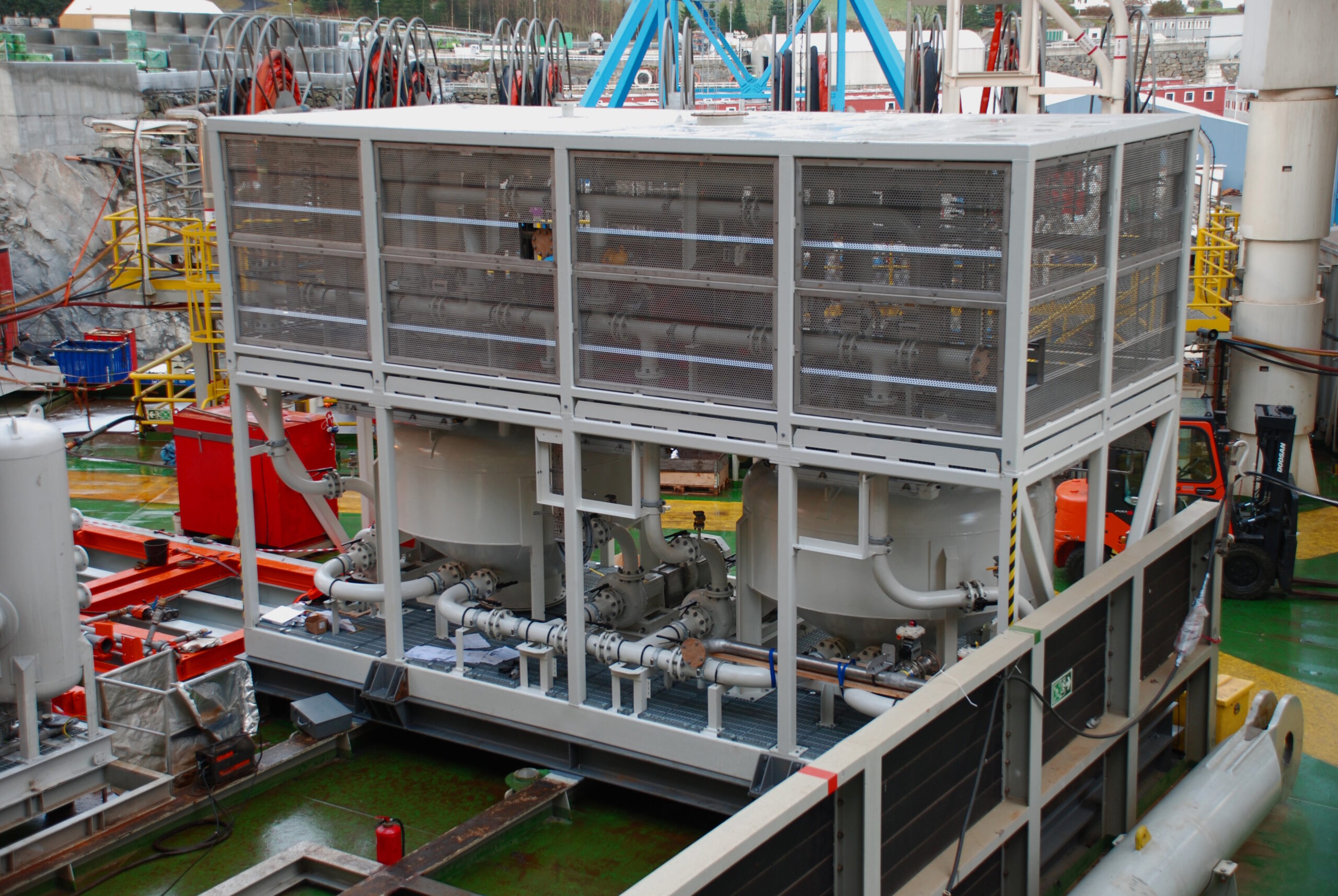
Streamlining Operational Processes
Streamlining operational processes is another key strategy for achieving cost-effective DCRI solutions. This involves optimizing the entire workflow, from cuttings collection and slurrification to injection and monitoring. Automated systems can be employed to reduce the need for manual intervention, thereby lowering labor costs and minimizing the risk of human error. Real-time monitoring and control systems can also enhance operational efficiency by providing instant feedback on key parameters, allowing for quick adjustments and preventing costly downtime.
Regular maintenance and proactive equipment management are essential for minimizing operational costs. Predictive maintenance techniques, such as vibration analysis and thermal imaging, can help identify potential issues before they lead to equipment failure, reducing repair costs and unplanned downtime. Additionally, training personnel to operate and maintain DCRI systems efficiently can further enhance cost-effectiveness.
Collaborative Approaches and Shared Infrastructure
Collaborative approaches and shared infrastructure can offer significant cost savings, particularly for operators working in the same region or field. By pooling resources and sharing injection wells, monitoring systems, and other infrastructure, operators can reduce individual capital and operational expenditures. Joint ventures or partnerships can also facilitate the sharing of expertise and best practices, further enhancing cost efficiency.
Regulatory bodies and industry associations can play a role in promoting collaborative approaches by providing guidelines and frameworks for shared infrastructure. This not only reduces costs but also encourages a more sustainable and coordinated approach to waste management in the offshore oil and gas industry.
Regulatory Compliance and Risk Management
While regulatory compliance is often viewed as a cost driver, it can also be a source of cost savings when managed effectively. Non-compliance with environmental regulations can result in hefty fines, legal challenges, and reputational damage, all of which can significantly impact the bottom line. By investing in robust compliance management systems and staying abreast of regulatory changes, operators can avoid these costs and ensure the long-term viability of their DCRI systems.
Risk management is another important aspect of cost-effective DCRI solutions. Conducting thorough risk assessments and implementing mitigation measures can prevent costly incidents such as well failures, spills, or contamination. Insurance and financial instruments can also be used to manage risk and protect against unforeseen expenses.
Conclusion
Cost-effective drill cuttings reinjection solutions are essential for operators seeking to balance environmental responsibility with financial efficiency. By optimizing injection well design and location, leveraging modular and scalable equipment, implementing energy-efficient technologies, streamlining operational processes, and adopting collaborative approaches, operators can significantly reduce the costs associated with DCRI systems. Additionally, proactive regulatory compliance and risk management can prevent costly incidents and ensure the long-term success of DCRI operations.
As the offshore oil and gas industry continues to face increasing pressure to adopt sustainable practices, cost-effective DCRI solutions offer a viable pathway for achieving environmental and economic goals. By embracing these strategies, operators can enhance their competitiveness, reduce their environmental footprint, and contribute to the sustainable development of the industry.