Drill cuttings reinjection (DCRI) is a sophisticated waste management technique widely used in the offshore oil and gas industry to handle the disposal of drill cuttings and associated drilling waste. This process involves grinding the cuttings into a fine slurry and injecting them into subsurface geological formations, effectively isolating the waste from the environment. DCRI systems are designed to be efficient, environmentally friendly, and compliant with stringent regulatory standards.
Overview of Drill Cuttings Reinjection
Drill cuttings are the fragmented pieces of rock generated during the drilling of oil and gas wells. These cuttings are typically mixed with drilling fluids, which can contain various chemicals and additives. Traditional disposal methods, such as offshore discharge or onshore landfill, pose significant environmental and regulatory challenges. Drill cuttings reinjection offers a sustainable alternative by securely containing the waste within subsurface formations, preventing environmental contamination and reducing the need for surface disposal.
Key Components of a DCRI System
A drill cuttings reinjection system consists of several key components that work together to process and inject the cuttings into the subsurface. These components include the cuttings collection and transfer system, the slurrification unit, the injection pump, and the monitoring and control system.
The cuttings collection and transfer system is responsible for gathering the drill cuttings from the drilling rig and transporting them to the slurrification unit. This system typically includes shakers, centrifuges, and conveyors that separate the cuttings from the drilling fluid and transfer them to the next stage of the process.
The slurrification unit is where the drill cuttings are ground into a fine slurry. This unit typically includes a grinding mill or similar equipment that reduces the cuttings to a particle size suitable for injection. The slurry is then mixed with water or other fluids to achieve the desired consistency and viscosity. Additives may be introduced to enhance the slurry’s properties, such as improving its pumpability or preventing clogging in the injection well.
The injection pump is a critical component of the DCRI system, responsible for pumping the slurry into the subsurface formation. High-pressure pumps are used to overcome the resistance of the geological formation and ensure that the slurry is injected at the required depth and pressure. The injection pump must be capable of handling the abrasive nature of the slurry and operating reliably under high-pressure conditions.
The monitoring and control system is essential for ensuring the safe and efficient operation of the DCRI system. This system includes sensors, gauges, and control panels that provide real-time data on parameters such as pressure, flow rate, and slurry density. The data is used to monitor the injection process, detect any anomalies, and make adjustments as needed to maintain optimal performance.
Operational Process of Drill Cuttings Reinjection
The operational process of drill cuttings reinjection involves several stages, from the collection of cuttings to their final injection into the subsurface. The process begins with the collection of drill cuttings from the drilling rig. The cuttings are separated from the drilling fluid using shakers and centrifuges, which remove the bulk of the fluid and prepare the cuttings for further processing.
Once collected, the cuttings are transferred to the slurrification unit, where they are ground into a fine slurry. The grinding process reduces the cuttings to a particle size that can be easily pumped and injected into the subsurface. The slurry is then mixed with water or other fluids to achieve the desired consistency and viscosity. Additives may be introduced to enhance the slurry’s properties, such as improving its pumpability or preventing clogging in the injection well.
The prepared slurry is then pumped into the injection well using high-pressure pumps. The injection well is typically drilled to a depth that allows the slurry to be injected into a suitable geological formation, such as a depleted reservoir or a deep saline aquifer. The injection process is closely monitored to ensure that the slurry is injected at the correct pressure and flow rate, and that the formation can accommodate the volume of slurry being injected.
During the injection process, real-time data on parameters such as pressure, flow rate, and slurry density is collected and analyzed. This data is used to monitor the injection process, detect any anomalies, and make adjustments as needed to maintain optimal performance. The monitoring and control system plays a crucial role in ensuring the safe and efficient operation of the DCRI system.
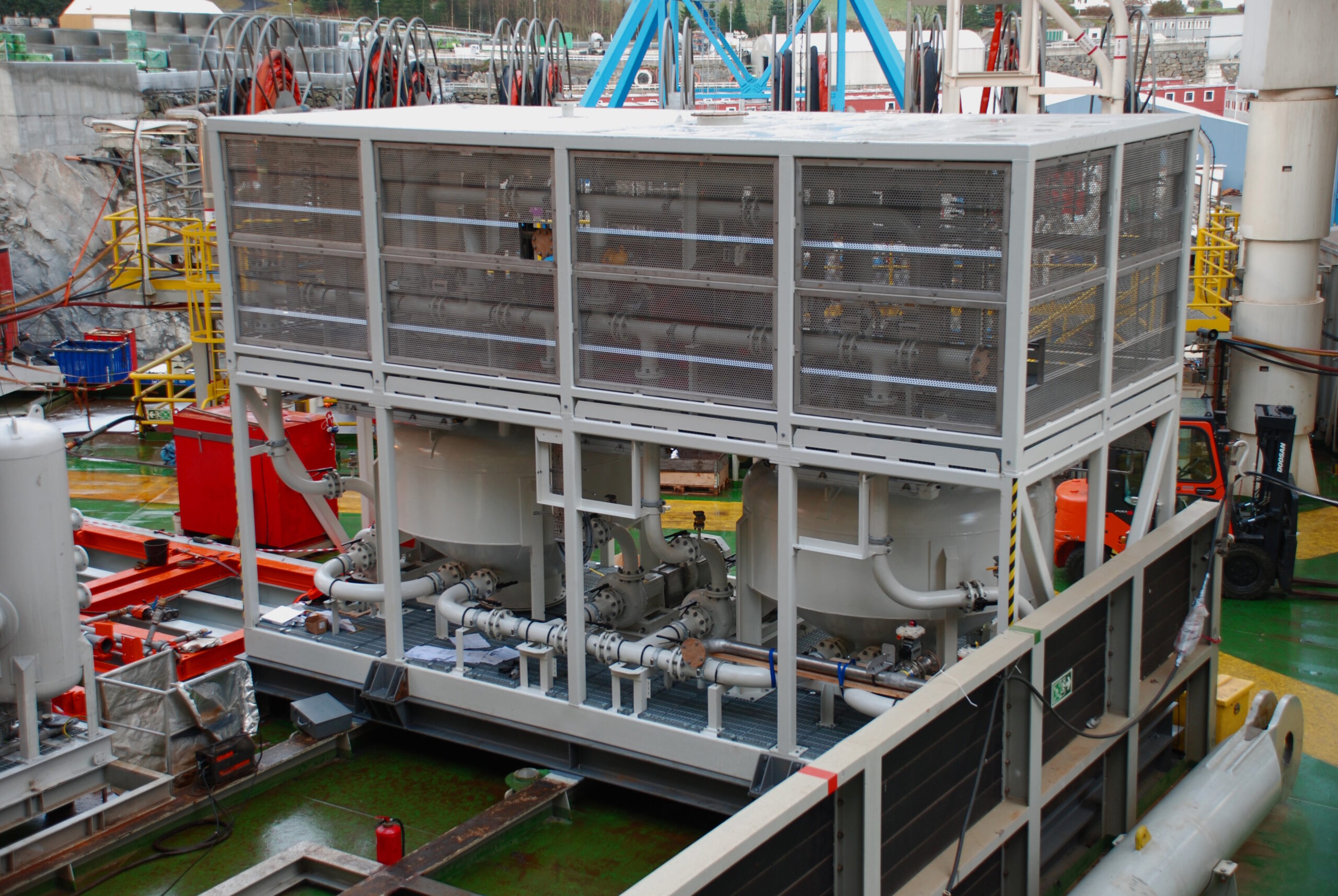
Technical Considerations and Challenges
The successful implementation of a drill cuttings reinjection system requires careful consideration of several technical factors. One of the primary considerations is the selection of the injection well and the target formation. The injection well must be drilled to a depth that allows the slurry to be injected into a suitable geological formation, such as a depleted reservoir or a deep saline aquifer. The target formation must have sufficient porosity and permeability to accommodate the volume of slurry being injected, and it must be isolated from freshwater aquifers and other sensitive formations to prevent contamination.
Another important consideration is the design and operation of the slurrification unit. The unit must be capable of grinding the cuttings to a particle size suitable for injection and mixing the slurry to achieve the desired consistency and viscosity. The abrasive nature of the cuttings can pose challenges for the grinding equipment, requiring the use of wear-resistant materials and regular maintenance to ensure reliable operation.
The injection pump is another critical component that requires careful consideration. The pump must be capable of operating under high-pressure conditions and handling the abrasive nature of the slurry. The design of the pump must also allow for easy maintenance and repair, as the abrasive nature of the slurry can lead to wear and tear over time.
The monitoring and control system is essential for ensuring the safe and efficient operation of the DCRI system. The system must be capable of providing real-time data on key parameters such as pressure, flow rate, and slurry density, and it must be able to detect and respond to any anomalies in the injection process. The system must also be designed to provide alerts and shutdowns in the event of a failure or emergency, ensuring the safety of personnel and equipment.
Environmental and Regulatory Compliance
Drill cuttings reinjection systems must comply with a range of environmental and regulatory standards to ensure their safe and responsible operation. These standards include guidelines set by organizations such as the International Maritime Organization (IMO) and the Environmental Protection Agency (EPA), as well as local regulations specific to the region where the system is being operated.
Compliance with these standards requires careful planning and design of the DCRI system, as well as ongoing monitoring and reporting of its operation. The system must be designed to prevent any release of cuttings or slurry into the environment, and it must include measures to detect and respond to any leaks or spills. Regular inspections and maintenance are also required to ensure the continued safe and efficient operation of the system.
Conclusion
Drill cuttings reinjection systems represent a significant advancement in waste management for the offshore oil and gas industry, offering a sustainable and environmentally responsible alternative to conventional disposal methods. By securely containing drill cuttings within subsurface geological formations, DCRI systems eliminate the risk of environmental contamination and reduce the need for surface disposal. The successful implementation of a DCRI system requires careful consideration of several technical factors, including the selection of the injection well, the design of the slurrification unit, and the operation of the injection pump and monitoring system. Compliance with environmental and regulatory standards is also essential to ensure the safe and responsible operation of the system. By adopting drill cuttings reinjection, oil and gas operators can achieve a more sustainable and efficient approach to waste management, contributing to the long-term success and sustainability of offshore operations.