Offshore cargo baskets are critical components in the oil and gas industry, designed to transport heavy, bulky, or irregularly shaped equipment and supplies to and from offshore installations. Given the harsh and demanding conditions of the offshore environment, regular inspection and maintenance of these baskets are essential to ensure their safety, reliability, and longevity. Proper inspection and maintenance practices not only prevent accidents and equipment failures but also ensure compliance with international standards and regulations.
Importance of Inspection and Maintenance
Offshore cargo baskets are subjected to extreme conditions, including exposure to saltwater, high winds, dynamic loads, and mechanical stresses during lifting and transportation. Over time, these factors can lead to wear and tear, corrosion, and structural degradation, compromising the safety and performance of the baskets. Regular inspection and maintenance are crucial to identify and address potential issues before they escalate into serious problems. This proactive approach helps to prevent accidents, reduce downtime, and extend the service life of the cargo baskets, ultimately contributing to the overall efficiency and safety of offshore operations.
Inspection Procedures
The inspection of offshore cargo baskets involves a thorough assessment of their structural integrity, safety features, and overall condition. Inspections should be conducted by qualified personnel with expertise in offshore equipment and should follow a systematic approach to ensure that all critical components are evaluated.
One of the primary areas to inspect is the structural framework of the cargo basket. This includes checking for signs of corrosion, cracks, or deformation in the steel or alloy components. Corrosion is a common issue in offshore environments due to the presence of saltwater, and it can significantly weaken the structure if left unaddressed. Inspectors should pay particular attention to weld joints, corners, and lifting points, as these areas are prone to stress and fatigue. Non-destructive testing (NDT) methods, such as ultrasonic testing, magnetic particle inspection, and dye penetrant testing, can be used to detect surface and subsurface defects that may not be visible to the naked eye.
The flooring of the cargo basket is another critical component to inspect. The floor, often made of steel grating or solid plates, must be checked for signs of wear, corrosion, or damage that could compromise its load-bearing capacity. Inspectors should ensure that the flooring is securely attached to the framework and that there are no loose or missing fasteners.
Lifting points, such as padeyes or lifting lugs, are essential for the safe handling of cargo baskets and must be inspected for signs of wear, deformation, or cracking. These components are subjected to significant stress during lifting operations, and any defects could lead to catastrophic failure. Inspectors should verify that the lifting points are properly aligned and that the load is evenly distributed during lifting.
Safety features, such as securing points and locking mechanisms, should also be inspected to ensure that they are functioning correctly. These features are critical for preventing cargo from shifting or falling out during transit, and any defects could pose a serious risk to personnel and equipment.
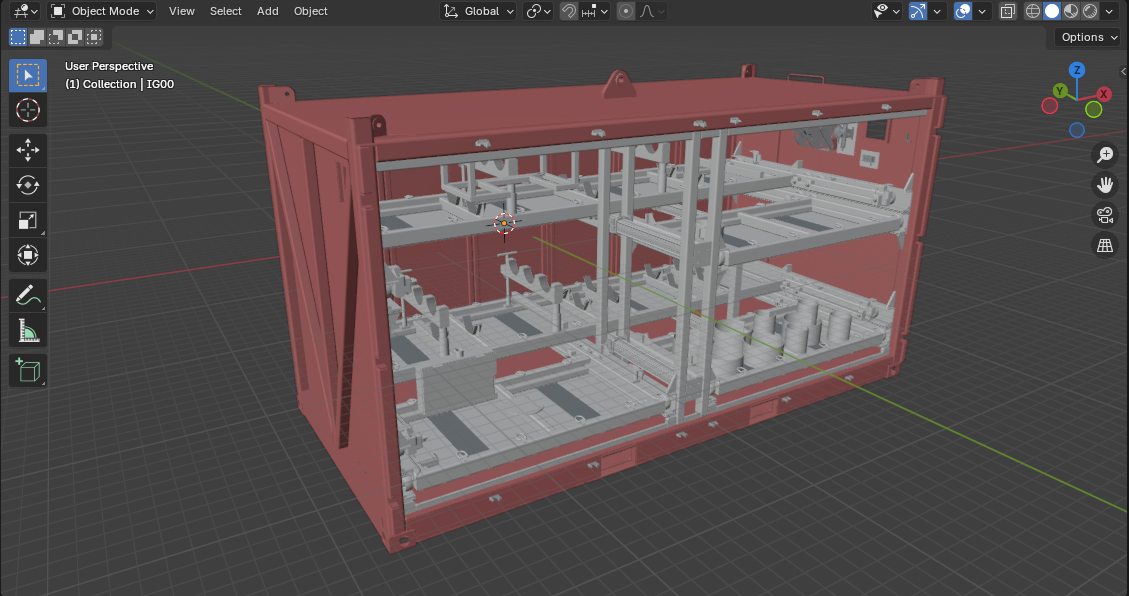
Maintenance Practices
Maintenance of offshore cargo baskets involves a combination of preventive and corrective actions to address identified issues and ensure the ongoing safety and performance of the equipment. Preventive maintenance focuses on routine tasks that help to prevent problems from occurring, while corrective maintenance involves repairing or replacing damaged or worn components.
One of the key preventive maintenance tasks is the regular cleaning of the cargo basket to remove salt, dirt, and other contaminants that can contribute to corrosion. Cleaning should be followed by the application of protective coatings, such as paint or anti-corrosion treatments, to shield the metal surfaces from the corrosive effects of the offshore environment. Inspectors should also lubricate moving parts, such as hinges and locking mechanisms, to ensure smooth operation and prevent wear.
Corrective maintenance involves addressing any issues identified during inspections. This may include repairing or replacing corroded or damaged components, reinforcing weak areas, or replacing worn lifting points. Welding repairs should be carried out by qualified welders using appropriate materials and techniques to ensure the structural integrity of the basket. Any repairs or modifications should be documented and verified through follow-up inspections to ensure that they meet the required standards.
Regulatory Compliance and Certification
Offshore cargo baskets must comply with a range of international standards and regulations to ensure their safety and reliability. These include standards set by organizations such as the International Organization for Standardization (ISO), the International Maritime Organization (IMO), and classification societies like Det Norske Veritas (DNV), the American Bureau of Shipping (ABS), and Lloyd’s Register. Compliance with these standards is verified through a rigorous certification process, which includes design review, material testing, and on-site inspections.
Regular inspections and maintenance are essential to maintain certification and ensure the ongoing safety and performance of the cargo baskets. Inspections should be conducted at regular intervals, as specified by the manufacturer or regulatory authorities, and should be documented in detail. Any issues identified during inspections must be addressed promptly, and the repairs or modifications should be verified through follow-up inspections.
Conclusion
Inspecting and maintaining offshore cargo baskets is a critical aspect of ensuring the safety, reliability, and efficiency of offshore operations. Regular inspections help to identify and address potential issues before they escalate into serious problems, while proactive maintenance practices help to prevent accidents, reduce downtime, and extend the service life of the equipment. By adhering to international standards and regulations, and by following best practices for inspection and maintenance, operators can ensure the safe and efficient transportation of equipment and supplies in some of the most demanding environments on Earth. The proactive care of offshore cargo baskets not only protects personnel and assets but also contributes to the overall success and sustainability of offshore operations.