Prefabricated offshore modules are a critical component in the oil and gas industry, offering a cost-effective, efficient, and sustainable solution for the construction, modification, and maintenance of offshore platforms. These modules are pre-engineered, pre-fabricated, and often repurposed or upgraded units that can be integrated into existing offshore structures or used to construct new facilities. They play a vital role in extending the lifespan of aging platforms, enhancing operational efficiency, and reducing downtime during upgrades or repairs.
Design and Functionality of Prefabricated Offshore Modules
Prefabricated offshore modules are designed to meet the specific requirements of offshore oil and gas platforms, which often operate in harsh and demanding environments. These modules can serve a variety of functions, including accommodation for personnel, housing for critical equipment, utility systems, and process units such as gas compression or oil separation. The design process begins with a thorough assessment of the platform’s needs, taking into account factors such as available space, load-bearing capacity, and environmental conditions.
The modules are typically constructed onshore in controlled environments, where quality control and precision engineering can be more effectively managed. This approach allows for the use of advanced fabrication techniques, such as modular construction and prefabrication, which ensure high levels of accuracy and consistency. The modules are built using durable materials, such as high-strength steel and corrosion-resistant alloys, to withstand the corrosive effects of saltwater, extreme weather, and dynamic loads.
One of the key design considerations for prefabricated modules is their modularity. This allows for easy transportation, installation, and integration with existing offshore structures. The modules are often designed with standardized interfaces and connectors, enabling seamless integration with the platform’s electrical, mechanical, and communication systems. This modularity also facilitates future upgrades or modifications, as additional modules can be added or existing ones replaced with minimal disruption to operations.
Applications of Prefabricated Offshore Modules
Prefabricated offshore modules are used in a wide range of applications across the oil and gas industry. One of the most common uses is in the upgrade or life extension of aging platforms. As offshore platforms age, their infrastructure may become outdated or insufficient to meet current operational demands. Preefabricated modules can be used to replace or augment existing facilities, providing modern, efficient, and reliable solutions without the need for complete platform replacement.
Another important application is in the construction of new offshore platforms. Prefabricated modules can be used to expedite the construction process, reducing the time and cost associated with traditional on-site construction. By fabricating the modules onshore and then transporting them to the offshore site, operators can significantly reduce the complexity and risks associated with offshore construction.
Prefabricated modules are also used in the development of floating production storage and offloading (FPSO) units. These units require a wide range of modules, including process modules, utility modules, and accommodation modules, to support their operations. Prefabricated modules provide a flexible and cost-effective solution for meeting these requirements, allowing FPSO operators to customize their facilities to suit specific project needs.
Benefits of Prefabricated Offshore Modules
The use of prefabricated offshore modules offers numerous benefits to the oil and gas industry. One of the most significant advantages is cost savings. By fabricating the modules onshore, operators can take advantage of lower labor and material costs, as well as reduced risks associated with offshore construction. Additionally, the use of standardized designs and components can further reduce costs by minimizing the need for custom engineering and fabrication.
Another key benefit is reduced downtime. Offshore platforms are critical assets, and any downtime can result in significant financial losses. Prefabricated modules can be quickly installed and integrated with existing facilities, minimizing the disruption to operations. This is particularly important for life extension projects, where the goal is to extend the operational life of the platform with minimal downtime.
Prefabricated modules also offer enhanced safety and quality control. By fabricating the modules in a controlled onshore environment, operators can ensure that the highest standards of safety and quality are maintained throughout the construction process. This reduces the risk of defects or failures that could compromise the safety and reliability of the offshore platform.
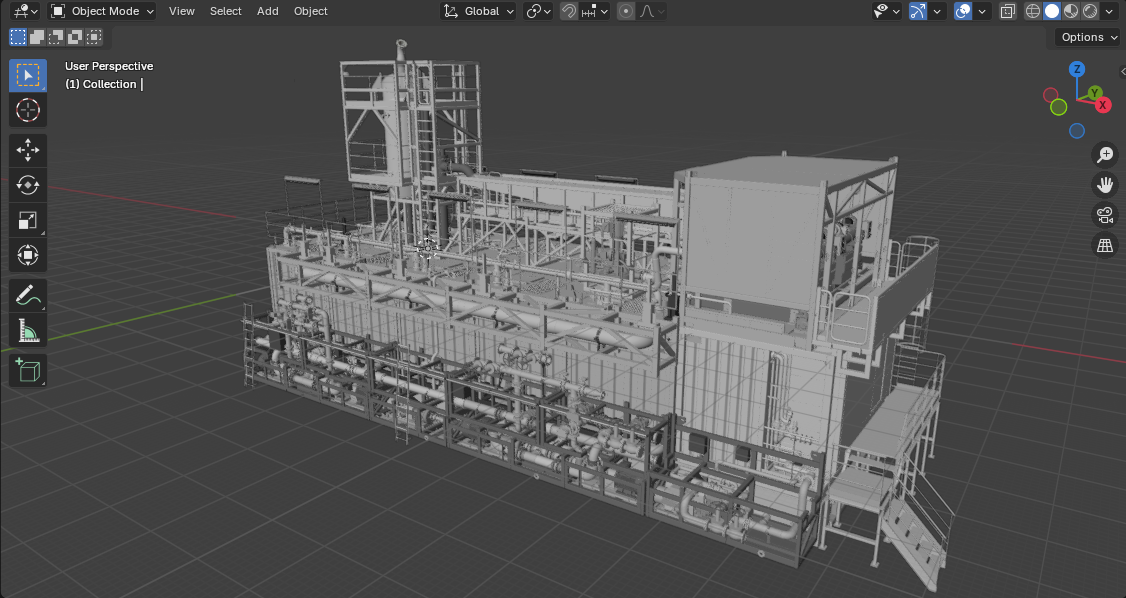
Engineering Considerations for Prefabricated Offshore Modules
The design and engineering of prefabricated offshore modules involve a number of critical considerations to ensure their safety, reliability, and performance. One of the primary considerations is structural integrity. The modules must be designed to withstand the dynamic loads and environmental conditions encountered in the offshore environment, including wave forces, wind loads, and seismic activity. Advanced simulation tools, such as finite element analysis (FEA), are often used to model the behavior of the modules under various load conditions and ensure that they meet the required safety and performance criteria.
Another important consideration is the integration of the modules with the existing offshore infrastructure. This includes ensuring compatibility with the platform’s structural design, as well as the seamless integration of electrical, mechanical, and communication systems. Custom interfaces and connectors are often developed to facilitate this integration, ensuring that the modules function as an integral part of the offshore installation.
Environmental considerations are also a key factor in the design and engineering of prefabricated modules. The modules must be designed to minimize their environmental impact, both during construction and operation. This includes the use of environmentally friendly materials, as well as the incorporation of energy-efficient systems and waste management solutions.
Regulatory Compliance and Certification
Prefabricated offshore modules must comply with a range of international standards and regulations to ensure their safety and reliability. These include standards set by organizations such as the International Maritime Organization (IMO), the American Bureau of Shipping (ABS), and Det Norske Veritas (DNV). Compliance with these standards is verified through a rigorous certification process, which includes design review, material testing, and on-site inspections.
The certification process ensures that the modules meet the highest standards of safety and quality, providing assurance to operators and personnel alike. Regular inspections and maintenance are also required to maintain certification and ensure the ongoing safety and performance of the modules throughout their service life.
Conclusion
Prefabricated offshore modules are a vital component in the oil and gas industry, offering a cost-effective, efficient, and sustainable solution for the construction, modification, and maintenance of offshore platforms. Their design and engineering involve a high degree of customization and adherence to stringent safety standards, ensuring that they can withstand the harsh offshore environment and meet the specific needs of each project.