Offshore containers play a crucial role in the transport and storage of equipment, tools, and materials in offshore environments. Selecting the right offshore container requires an understanding of operational requirements, environmental challenges, compliance standards, and durability considerations. The selection process must take into account factors such as structural integrity, certification, loading capacity, corrosion resistance, and safety features.
Material and Structural Considerations
The construction material of an offshore container is a key factor influencing its performance in harsh maritime environments. Steel is commonly used due to its high strength and resistance to impact loads. Corrosion-resistant coatings and specialized alloys are often employed to enhance longevity. The structural framework must be reinforced to withstand dynamic loads during lifting and transportation, ensuring that deformation does not compromise integrity. Welding techniques and corner casting designs should conform to regulatory standards, preventing structural failure during offshore operations.
Regulatory Compliance and Certification
All offshore containers must meet stringent certification requirements to ensure operational safety. Regulatory bodies such as DNV, Lloyd’s Register, and ABS provide guidelines for design, manufacturing, and periodic inspection. The certification process involves load testing, non-destructive examination of welds, and assessment of lifting points. Compliance with international standards such as DNV 2.7-1, EN 12079, and ISO 10855 is mandatory for safe deployment in offshore applications. Containers must be marked with identification plates displaying certification details, including maximum gross weight, safe working load, and date of last inspection.
Environmental and Corrosion Resistance Factors
The offshore environment presents challenges such as saltwater exposure, extreme temperatures, and high humidity levels. These factors accelerate corrosion, which can compromise the structural integrity of containers. Protective coatings, galvanization, and cathodic protection methods are employed to mitigate corrosion-related deterioration. Container designs must account for drainage and ventilation to prevent water accumulation, which can lead to accelerated degradation. Material selection must align with environmental conditions to ensure prolonged service life and minimal maintenance requirements.
Load Capacity and Operational Efficiency
Determining the appropriate load capacity of an offshore container is critical to maintaining safety and efficiency. Containers are designed for specific weight limits, and exceeding these can lead to structural failure. The load-bearing components, including the base frame and lifting lugs, must be engineered to handle anticipated loads with a suitable safety margin. Internal layout and load-securing mechanisms, such as tie-down points and cargo netting, contribute to operational efficiency by preventing shifting during transport. Proper weight distribution and center of gravity considerations further enhance stability during lifting and offshore handling.
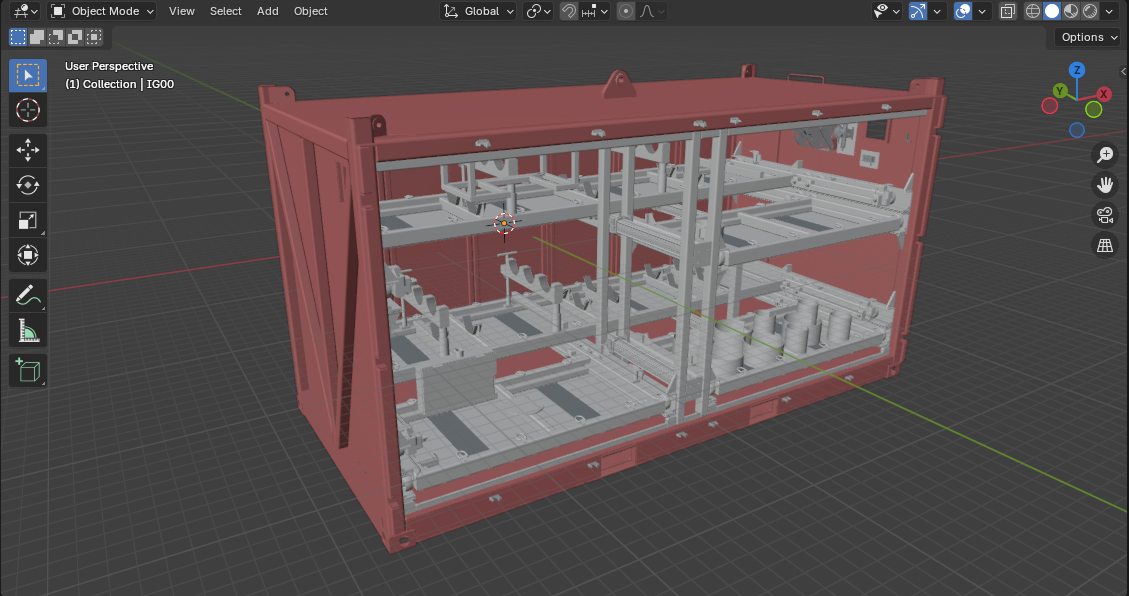
Specialized Container Types and Applications
Offshore containers are available in various configurations to meet diverse operational needs. Cargo baskets are commonly used for transporting irregularly shaped equipment, while closed containers provide secure storage for sensitive materials. Reefer containers are designed for temperature-controlled cargo, ensuring that perishable goods remain viable during transport. Specialized containers, such as hazardous material storage units and workshop containers, cater to industry-specific requirements. The selection of a container type should be guided by the intended application, ensuring that functionality aligns with operational demands.
Lifting and Handling Safety Measures
Offshore container lifting operations involve dynamic forces that necessitate stringent safety measures. Lifting points must be engineered to accommodate the stresses encountered during hoisting. Shackles, slings, and pad eyes should be rated for offshore use and undergo periodic inspections to detect wear and fatigue. The stability of the container during lifting must be maintained through balanced weight distribution and secure attachment to lifting equipment. Drop testing and impact assessments form part of the quality assurance process to validate resilience under operational conditions.
Inspection and Maintenance Protocols
Routine inspections are essential to maintain the safety and functionality of offshore containers. Periodic assessments focus on structural integrity, corrosion damage, and wear of lifting components. Load testing is conducted to verify continued compliance with weight capacity ratings. Repair procedures must follow regulatory guidelines, with certified personnel performing welding and structural reinforcements. Documentation of inspection results, maintenance activities, and certification renewals is a critical aspect of regulatory compliance and operational accountability.
Conclusion
The selection of offshore containers is a multifaceted process that requires consideration of material properties, structural design, regulatory compliance, environmental resistance, and operational safety. Ensuring that containers meet industry standards minimizes risks and enhances efficiency in offshore logistics.