Offshore containers represent a critical component in maritime and offshore operations, designed specifically to withstand the harsh conditions of marine environments while facilitating the safe transport of equipment, materials, and supplies to and from offshore installations.
Standard Offshore Containers
Standard offshore containers form the backbone of offshore logistics operations. These units are built to DNV 2.7-1 and EN12079 standards, incorporating robust construction methods with primary structural members manufactured from high-grade steel. The standard configurations typically feature dimensions of 8ft x 8ft or 8ft x 10ft footprints, with heights varying between 8ft and 10ft. These containers incorporate specialized lifting points, typically comprising pad eyes welded to the top corners, designed to withstand dynamic loads of up to 3g in offshore lifting operations.
The framework employs hollow section steel members, with corner posts and top and bottom side rails forming a rigid structure. The floor construction consists of steel checker plate or timber, supported by cross members, capable of supporting significant point loads. These containers incorporate drainage holes at the base corners and are equipped with fork pockets for handling when empty.
Specialized Variations
Tank Containers
Offshore tank containers serve the crucial function of transporting and storing liquids and chemicals in offshore environments. These units incorporate a pressure vessel housed within a standard container frame, complete with additional safety features such as pressure relief valves, temperature monitoring systems, and specialized filling and discharge connections. The tanks are typically constructed from stainless steel or specialized corrosion-resistant materials, depending on the intended cargo.
Half Height Containers
Half height containers address specific operational requirements where vertical clearance is limited or when transporting dense materials like drill cuttings or heavy equipment. These units maintain the standard footprint but feature reduced height, typically 4ft to 6ft. Despite their reduced height, they maintain the same structural integrity and lifting capacity as full-height units, often incorporating additional reinforcement in the base structure to handle concentrated loads.
Special Purpose Containers
Workshop Containers
Workshop containers are modified to serve as mobile maintenance facilities offshore. These units incorporate additional features such as workbenches, tool storage systems, electrical installations, and sometimes specialized ventilation systems. The interior typically features reinforced mounting points for equipment installation and may include additional door access points for improved functionality.
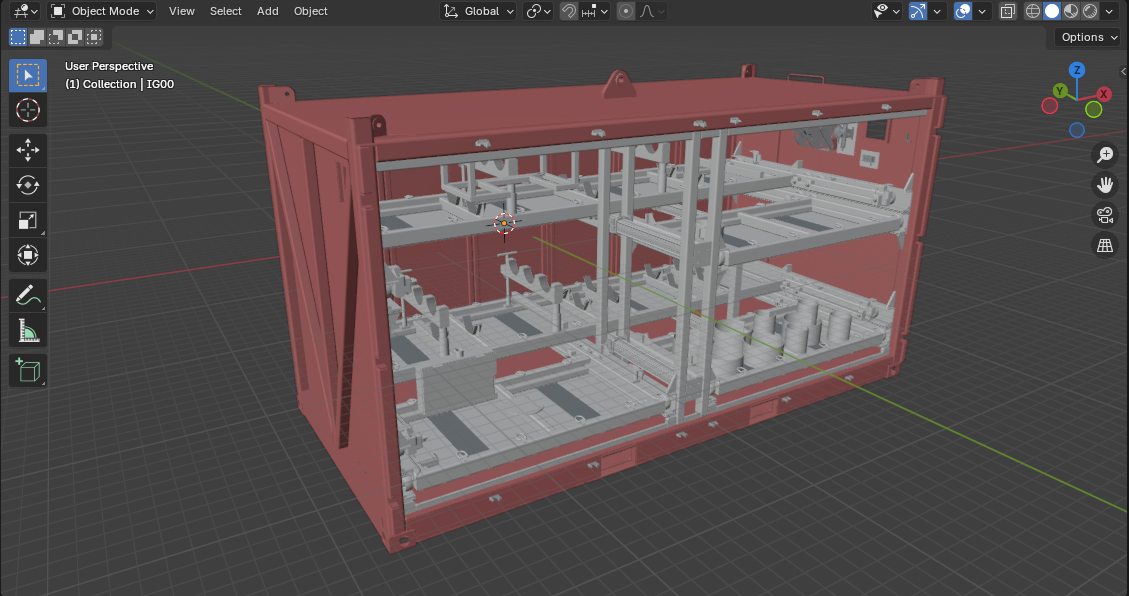
Laboratory Containers
Laboratory containers support offshore testing and analysis operations. These specialized units feature enhanced insulation, climate control systems, and specific interior layouts to accommodate laboratory equipment. They often incorporate specialized electrical systems, ventilation, and safety features appropriate for handling testing materials and chemicals.
Safety and Certification Requirements
All offshore containers must comply with rigorous safety standards and certification requirements. The primary certification standard DNV 2.7-1 mandates specific design criteria, including:
- Structural integrity requirements specifying minimum material thicknesses and weld specifications
- Load testing protocols for prototype and production units
- Documentation requirements including material certificates and testing records
- Periodic inspection and recertification requirements
Additionally, containers must maintain clear identification markings showing the maximum gross weight, tare weight, and payload capacity. These markings must remain visible throughout the container’s service life and comply with standardized placement requirements.
Maintenance and Inspection
Effective maintenance programs for offshore containers involve regular inspections and repairs to ensure continued safe operation. The inspection regime typically includes:
- Initial visual inspections before each use to identify obvious damage or deterioration
- Quarterly detailed inspections of lifting points and primary structure
- Annual thorough examinations including non-destructive testing of critical welds
- Four-yearly proof load testing and comprehensive structural assessment
Documentation of these inspections must be maintained throughout the container’s service life, with clear procedures for removing damaged units from service until repairs can be completed and verified.
Future Developments
The offshore container industry continues to evolve with emerging technologies and operational requirements. Current development trends include:
- Integration of smart monitoring systems to track container location and condition
- Development of lightweight materials maintaining required strength characteristics
- Enhanced modular designs allowing for rapid reconfiguration based on operational needs
- Implementation of improved corrosion protection systems extending service life
These developments promise to enhance the efficiency and safety of offshore container operations while reducing operational costs and environmental impact.
Conclusion
Offshore containers represent a crucial element in offshore operations, with their design and construction reflecting the demanding requirements of the marine environment. The variety of specialized containers available demonstrates the industry’s ability to adapt these units to specific operational requirements while maintaining the highest safety standards. Continued development in this field promises to further enhance the capability and efficiency of offshore container operations.