A drill cuttings handling system is designed to manage and transport the solid waste generated during drilling operations. These systems are particularly valuable in oil and gas exploration, where drill cuttings must be efficiently removed to ensure smooth operations and compliance with environmental standards. Below is a detailed description of its functionality and components:
Broadly speaking, the most significant highlights of this type of storage system are as follows:
A) Functionality:
Cuttings Collection: Drill cuttings are collected from the drilling fluid return line or shaker screens at the wellsite. The collected cuttings are typically separated from drilling mud to reduce waste fluid volume.
Air-Powered Conveyance: Compressed air is used to pneumatically transport the drill cuttings through pipelines or ducts. The system creates a high-velocity air stream that carries the cuttings from the point of collection to storage or disposal.
Cuttings Transport: Drill cuttings are transported to designated locations such as cuttings skips, bins, or processing units for further treatment, reuse, or disposal. The system may also facilitate long-distance conveyance for centralized processing.
Environmental Management: Ensures proper handling of waste material to minimize spillage, contamination, or environmental harm. Can be used in conjunction with cuttings dryers, thermal desorption units, or reinjection systems to further reduce waste volume or recover valuable drilling fluids.
B) Major components:
Cuttings Hopper: Collects the drill cuttings from shakers or other separation equipment. Often equipped with level sensors to regulate feed rates.
Pneumatic Conveying System: A network of pipelines, nozzles, and air movers that uses compressed air to move cuttings. Includes flow-control mechanisms to ensure steady transport.
Air Compressors: Generate the compressed air required for pneumatic conveying. May include high-pressure or low-pressure units, depending on the system’s requirements.
Cyclones or Separators (optional): Installed at the discharge end to separate the drill cuttings from the air stream. Allow clean air to be vented or recycled while retaining the solid particles.
Cuttings Storage Unit: Includes skips, tanks, or bins to hold cuttings temporarily before processing or disposal. Alternatively, active units or systems can be installed inline to directly treat the cuttings prior to their disposal.
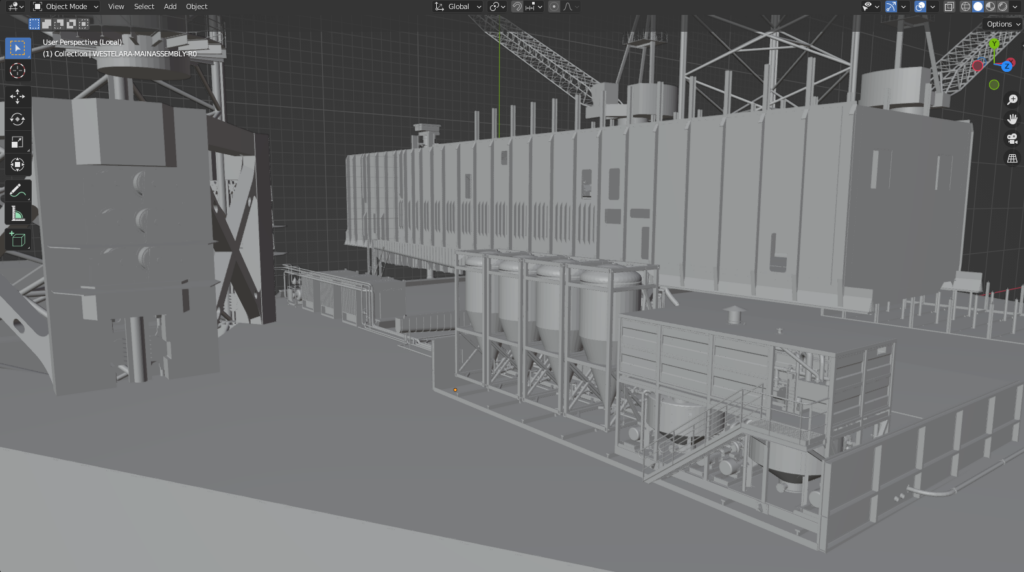
We can provide the following engineering services associated with the design and installation of a drill cuttings handling system.
- Feasibility Study and Concept Design:
- Rig-specific analysis for system integration
- Evaluation of space availability and weight considerations
- Preliminary process flow diagrams
- Conceptual layout designs
- Initial cost estimates and project timeline
- Detailed Engineering Design:
- Process engineering and equipment sizing
- Piping and Instrumentation Diagrams (P&IDs)
- 3D modeling of the system layout
- Structural analysis for rig modifications
- Electrical system design and integration
- Equipment Specification and Procurement Support:
- Development of technical specifications for major equipment
- Vendor evaluation and selection assistance
- Review of vendor documentation and drawings
- Structural Modifications Design:
- Design of new foundations or support structures for equipment
- Reinforcement designs for existing structures if required
- Finite Element Analysis (FEA) for critical structural components
- Integration Engineering:
- Interface design with existing rig systems
- Modification of existing piping systems
- Safety and Risk Engineering:
- Hazard and Operability (HAZOP) studies
- Failure Mode and Effects Analysis (FMEA)
- Safety Integrity Level (SIL) assessment
- Explosion risk assessment and zoning studies
- Regulatory Compliance and Classification:
- Liaison with classification societies
- Preparation of documentation for class approval
- Development of operational procedures to meet regulatory requirements
- Installation Planning:
- Development of detailed installation procedures
- Creation of work packages for shipyard or offshore installation
- Lift plans for major equipment
- Installation sequence optimization
- Commissioning and Start-up Support:
- Development of commissioning procedures
- Supervision of installation and commissioning activities
- Performance of system tests and trials
- Troubleshooting and optimization support
- Documentation and Training:
- Preparation of operating and maintenance manuals
- Development of crew training programs
- Environmental Impact Assessment:
- Support for environmental permit applications
- Project Management:
- Overall project scheduling and coordination
- Cost control and progress reporting
- Quality assurance and control
- Lifecycle Support:
- Development of maintenance and inspection schedules
- Optimization studies for long-term operation
- Technical support for system upgrades or modifications
- Feasibility Study and Concept Design:
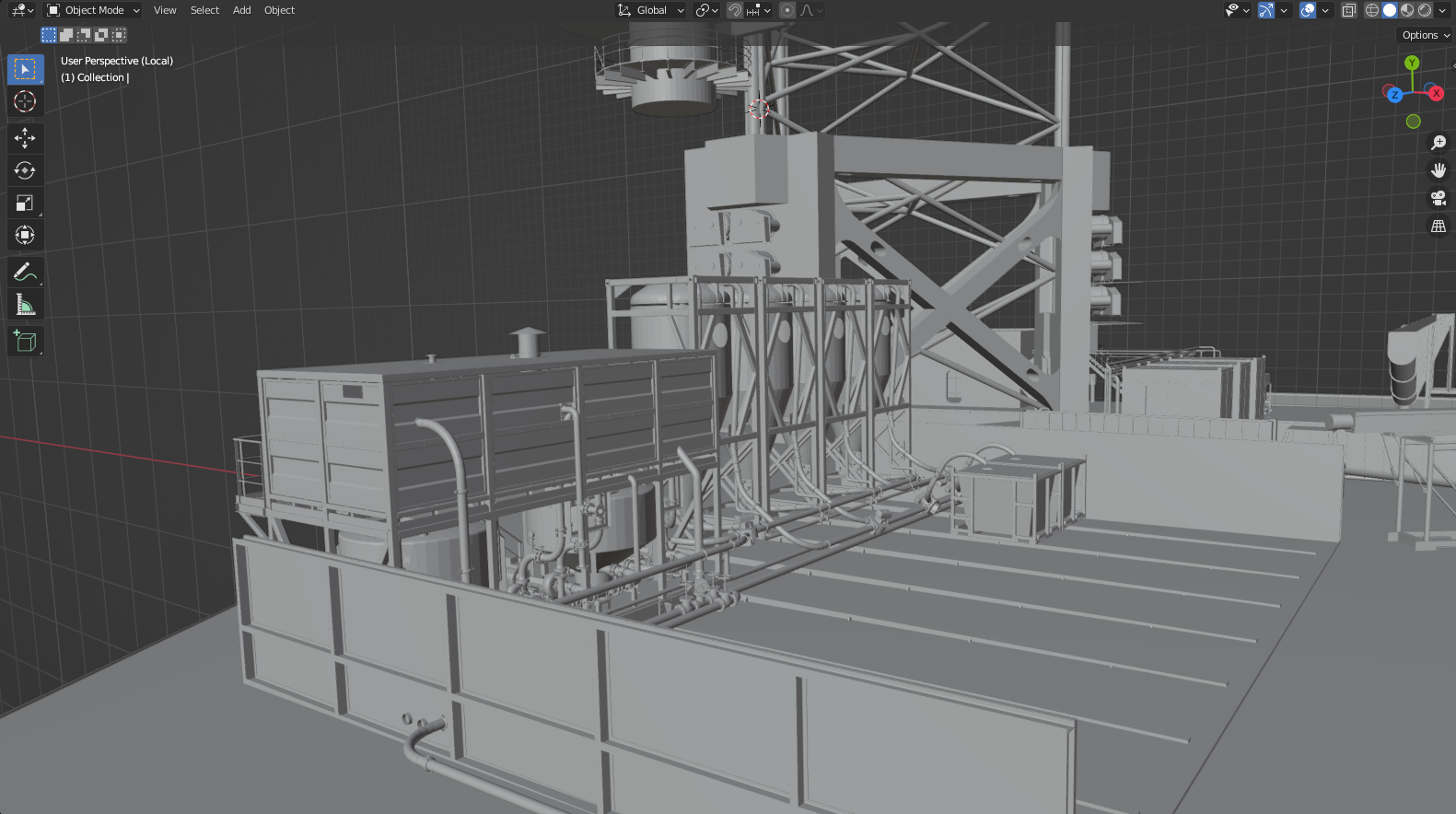
Please follow this link to download our brochure showcasing typical scopes of supply.