Chemical storage skids are essential modular units in offshore facilities, designed for the safe storage and controlled injection of process chemicals.
Chemical storage skids are self-contained units that integrate storage, containment, and injection systems for process chemicals used in offshore operations. These units are designed to meet stringent safety standards while ensuring reliable chemical delivery to process systems.
Broadly speaking, the most significant highlights of this type of storage system are as follows:
- Safe containment and storage of process chemicals
- Controlled chemical injection into process systems
- Secondary containment for spill prevention
- Chemical level monitoring and management
- Safe access for maintenance and refilling
- Storage tanks
- Secondary containment basin or tray
- Transfer / circulation pumps and distribution manifold
- Level sensors and gauges
- Safety relief valves
- Loading/unloading connections
- Control panel
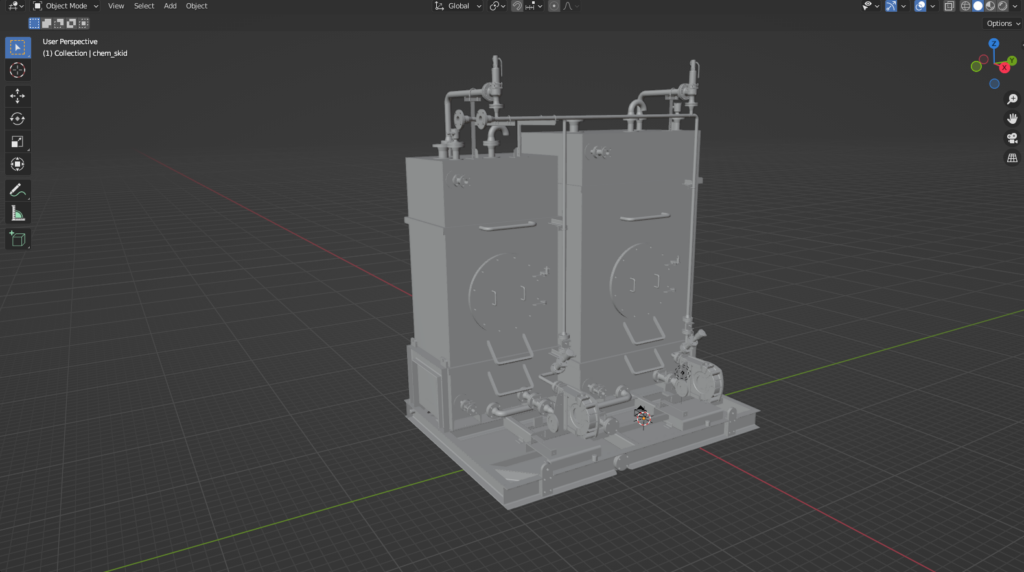
We can provide the following engineering services associated with the design and installation of modular skids for storage of chemical products.
- Feasibility Study and Concept Design:
- Rig-specific analysis for system integration
- Evaluation of space availability and weight considerations
- Preliminary process flow diagrams
- Conceptual layout designs
- Initial cost estimates and project timeline
- Detailed Engineering Design:
- Process engineering and equipment sizing
- Piping and Instrumentation Diagrams (P&IDs)
- 3D modeling of the system layout
- Structural analysis for rig modifications
- Electrical system design and integration
- Equipment Specification and Procurement Support:
- Development of technical specifications for major equipment
- Vendor evaluation and selection assistance
- Review of vendor documentation and drawings
- Structural Modifications Design:
- Design of new foundations or support structures for equipment
- Reinforcement designs for existing structures if required
- Finite Element Analysis (FEA) for critical structural components
- Integration Engineering:
- Interface design with existing rig systems
- Modification of existing piping systems
- Safety and Risk Engineering:
- Hazard and Operability (HAZOP) studies
- Failure Mode and Effects Analysis (FMEA)
- Safety Integrity Level (SIL) assessment
- Explosion risk assessment and zoning studies
- Regulatory Compliance and Classification:
- Liaison with classification societies
- Preparation of documentation for class approval
- Development of operational procedures to meet regulatory requirements
- Installation Planning:
- Development of detailed installation procedures
- Creation of work packages for shipyard or offshore installation
- Lift plans for major equipment
- Installation sequence optimization
- Commissioning and Start-up Support:
- Development of commissioning procedures
- Supervision of installation and commissioning activities
- Performance of system tests and trials
- Troubleshooting and optimization support
- Documentation and Training:
- Preparation of operating and maintenance manuals
- Development of crew training programs
- Environmental Impact Assessment:
- Support for environmental permit applications
- Project Management:
- Overall project scheduling and coordination
- Cost control and progress reporting
- Quality assurance and control
- Lifecycle Support:
- Development of maintenance and inspection schedules
- Optimization studies for long-term operation
- Technical support for system upgrades or modifications
- Feasibility Study and Concept Design:
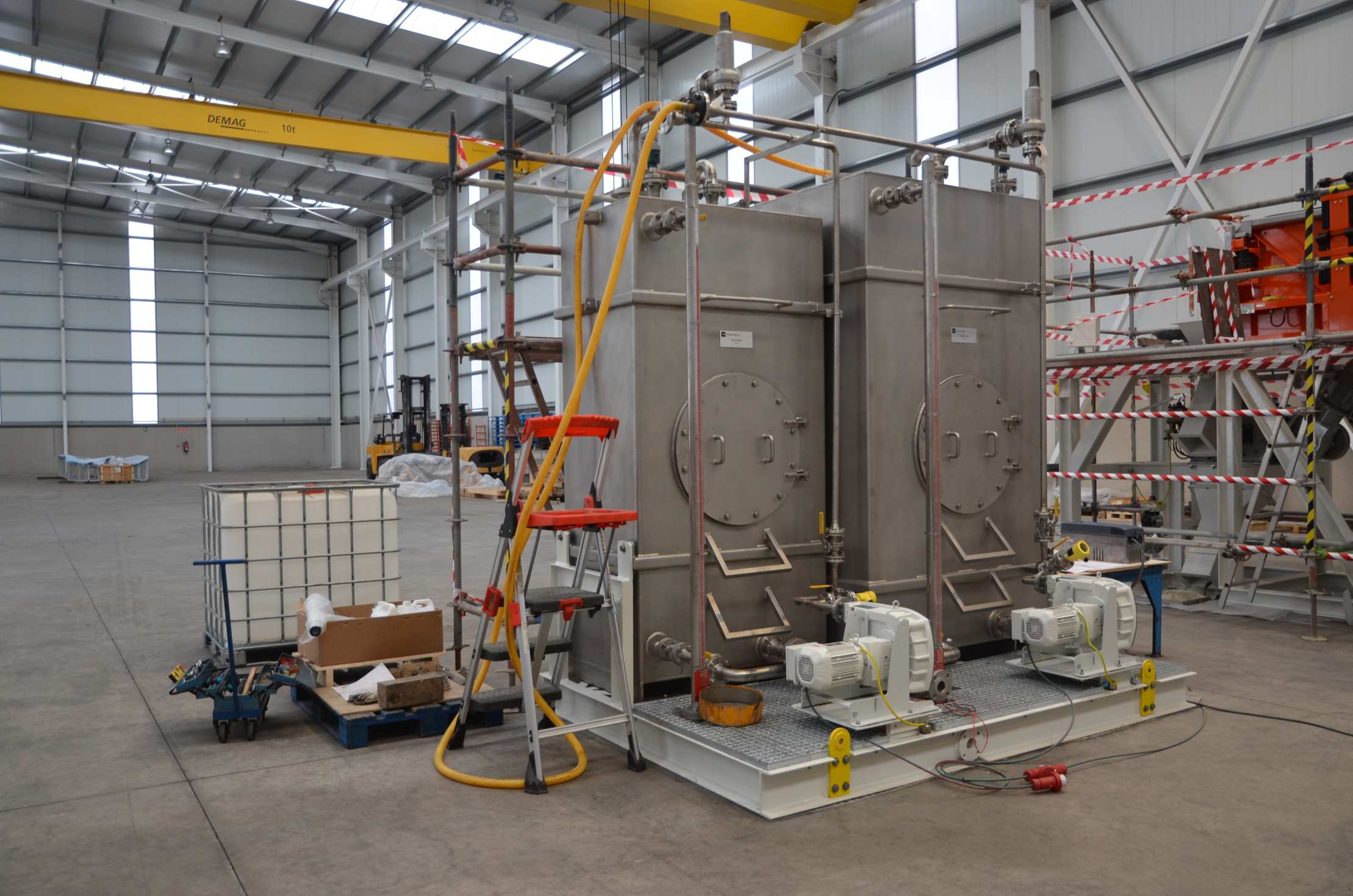
Please follow this link to download our brochure showcasing typical scopes of supply.