Exhaust Gas Cleaning Systems (EGCS), commonly known as scrubbers, are designed to reduce the emissions of sulfur oxides (SOx) and particulate matter from ship exhaust gases. These systems are critical for ensuring compliance with international maritime regulations, such as the IMO 2020 sulfur cap, which limits the sulfur content in marine fuels.
A scrubber is a complex system integrated into the ship’s exhaust system. It functions by treating the exhaust gases produced by the ship’s engines, boilers, and generators before they are released into the atmosphere.
Scrubbers enable ships to use higher-sulfur fuels while still complying with international emissions regulations. By reducing SOx emissions, scrubbers help to mitigate the environmental impact of shipping, contributing to cleaner air and a healthier marine environment.
However, it is important to consider the potential environmental impact of wash water discharge, particularly in sensitive or enclosed areas, which is why the choice between open-loop, closed-loop, and hybrid systems must be carefully considered based on the ship’s operating areas.
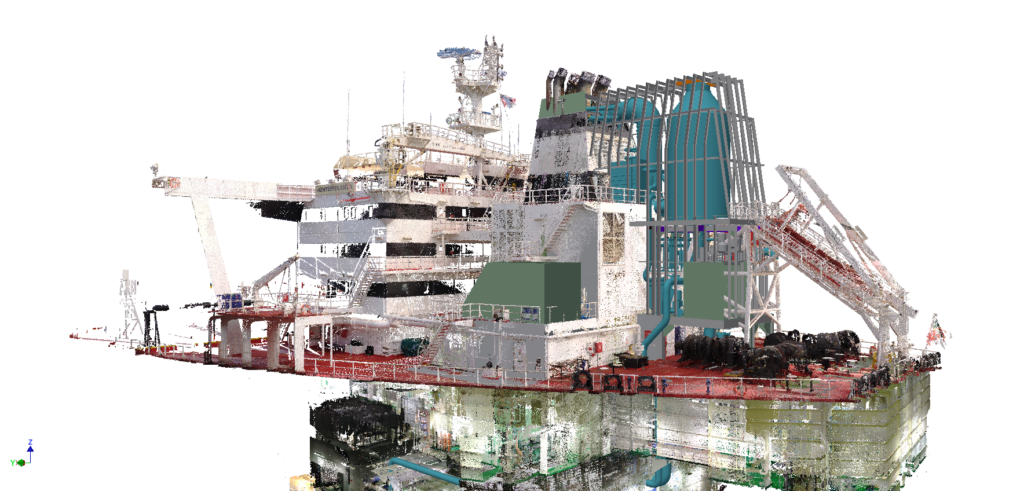
The three main types—open-loop, closed-loop, and hybrid scrubbers—each offer distinct advantages and applications.
Open-loop scrubbers are cost-effective and suitable for use in open ocean waters, closed-loop systems provide compliance in sensitive or regulated waters, and hybrid scrubbers offer flexibility for ships operating in diverse environments. The choice of scrubber depends on the ship’s operating regions, environmental regulations, and the owner’s commitment to environmental sustainability.
A. Open-Loop Scrubbers
Open-loop scrubbers use seawater directly to remove SOx from the exhaust gases. The exhaust gases are funneled through the scrubber tower, where they come into contact with seawater. The sulfur oxides react with the seawater, forming sulfuric acid, which is then neutralized by the natural alkalinity of the seawater.
The treated water, now containing neutralized sulfur compounds, is discharged back into the ocean, provided it meets environmental discharge standards.
Open-loop scrubbers are commonly used on ships operating in areas with high alkalinity seawater, such as open oceans, where the environmental impact of discharging treated water is minimal. They are relatively simple in design and operation, with lower installation and operating costs compared to other types of scrubbers. Their use is restricted in certain areas, such as coastal waters, ports, and sensitive environmental regions, where discharge regulations are stricter.
B. Closed-Loop Scrubbers
Closed-loop scrubbers use a recirculating water system, typically with an alkaline additive (e.g., sodium hydroxide), to neutralize sulfur oxides in the exhaust gases. The treated water is then reused in the system after passing through a water treatment unit.
Unlike open-loop systems, closed-loop scrubbers do not discharge process water into the sea. Instead, they retain the wash water on board, treating and reusing it, with only a minimal amount of sludge or waste that needs to be disposed of at port facilities.
Closed-loop scrubbers are ideal for vessels operating in areas with strict environmental regulations, such as coastal waters, ports, and emission control areas (ECAs). They provide greater flexibility in complying with discharge regulations and are effective in all types of water conditions, including freshwater and low alkalinity seawater.
Closed-loop systems are more complex and costly to install and operate due to the need for additional components, such as a water treatment system and storage tanks for sludge and treated water.
C. Hybrid Scrubbers
Hybrid scrubbers combine the features of both open-loop and closed-loop systems, allowing the operator to switch between modes depending on the ship’s location and environmental regulations. In open-loop mode, the system operates like a traditional open-loop scrubber, using seawater for scrubbing and discharging the treated water overboard. In closed-loop mode, the system recirculates and treats the wash water internally, with no discharge to the sea.
The ability to switch between modes provides operational flexibility, enabling compliance with varying regional and global environmental regulations.
Hybrid scrubbers are suitable for vessels that operate in diverse regions, including areas with stringent discharge regulations and open waters where discharge is permitted. They offer the benefits of both open-loop and closed-loop systems, providing operational flexibility and ensuring compliance with a wide range of environmental regulations. Hybrid systems are typically more expensive to install and maintain due to their complexity and the need for additional components.
Exhaust gas cleaning systems, or scrubbers, play a vital role in reducing sulfur oxide emissions from ships, helping the maritime industry meet stringent environmental regulations.
The cleaning process can be summarized as follows:
a) Gas Cooling and Saturation:
- Hot exhaust gas enters the scrubber and is cooled by water spray
- Gas is saturated with water vapor, improving scrubbing efficiency
b) SOx Removal:
- In open-loop systems, seawater’s natural alkalinity neutralizes SOx
- In closed-loop systems, alkaline chemicals (usually sodium hydroxide) are added to neutralize SOx
- SOx reacts with water to form sulfurous and sulfuric acids, which are then neutralized
c) Particulate Matter Removal:
- Water droplets capture particulates through impaction, interception, and diffusion.
- Larger particulates are removed more efficiently than smaller ones
d) Mist Elimination:
- Demister or mist eliminator removes water droplets from the cleaned gas
e) Water Treatment (for open-loop and hybrid systems):
- Contaminated water is treated to remove suspended particulates and adjust pH
- Oil content is reduced to comply with discharge regulations
- Treated water is monitored for compliance before discharge
f) Sludge Handling:
- Accumulated sludge is collected and stored for onshore disposal
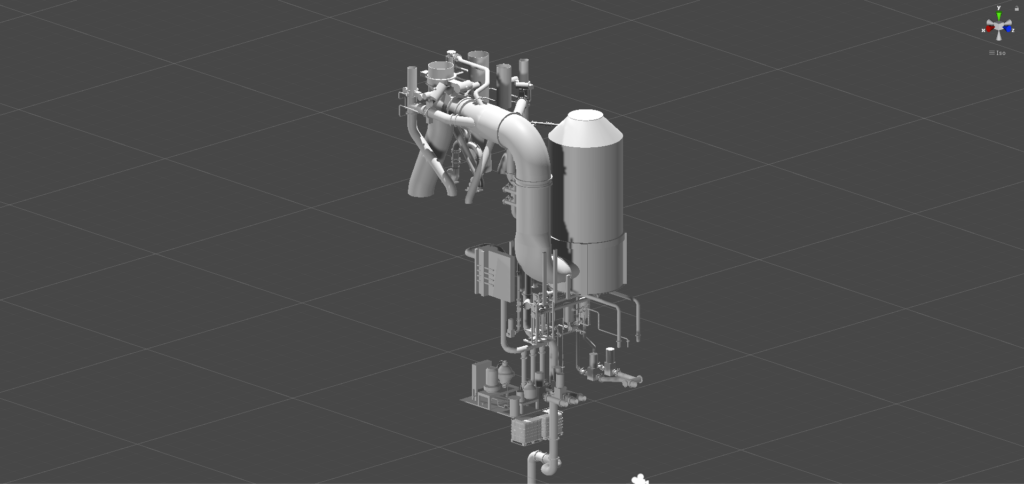
We can provide the following engineering services associated with the design and installation of EGCS systems.
- Feasibility Studies and System Selection:
- Vessel-specific analysis to determine optimal system
- Evaluation of available technologies considering vessel type, size, and trading patterns
- Cost-benefit analysis of different systems
- Regulatory compliance assessment
- System Design and Integration:
- Detailed engineering drawings and 3D modeling
- Piping and instrumentation diagrams (P&IDs)
- Electrical system design and integration
- Integration with ship’s existing systems
- Structural modifications design if required
- Installation Planning:
- Development of installation procedures and sequences
- Creation of work packages for shipyard or riding crew
- Dry-dock planning and scheduling
- Risk assessments and mitigation strategies
- Retrofit Engineering:
- Laser scanning of existing spaces for accurate 3D modeling
- Design of structural modifications to accommodate the EGCS
- Relocation design for existing systems to create space for the EGCS
- Conversion of existing tanks for EGCS chemical storage if applicable, or design of new chemical storage tanks
- Computational Fluid Dynamics (CFD) Analysis:
- Flow analysis in discharge pipes and treatment units
- Optimization of sampling points locations
- Commissioning and Testing Support:
- Development of commissioning procedures
- Oversight of installation and commissioning process
- Performance of sea trials and operational tests
- Troubleshooting and system optimization
- Documentation and Training:
- Preparation of updated vessel documentation
- Development of operation and maintenance manuals
- Creation of crew training materials and programs
- Regulatory Compliance Support:
- Preparation of documents for class approval
- Liaison with classification societies
- Assistance with type approval process if developing new EGCS
- Project Management:
- Overall project scheduling and coordination
- Cost control and progress reporting
- Quality assurance and control
- Life Cycle Support:
- Development of planned maintenance schedules
- Failure mode and effects analysis (FMEA)
- Spare parts optimization studies
- Feasibility Studies and System Selection:
These engineering services, in line with best practices in the industry, cover the entire lifecycle of EGCS projects, from initial concept to installation and ongoing support, ensuring compliant and efficient exhaust gas cleaning systems for vessels.
Please follow this link to download our brochure showcasing typical scopes of supply.