Digital Twin technology has emerged as a transformative tool in the marine and oil & gas industries, revolutionizing asset management, operational efficiency, and decision-making. A Digital Twin is a virtual replica of a physical asset, process, or system, continuously updated with real-time data and integrated with advanced analytics, machine learning, and simulation capabilities. This enables operators to monitor, optimize, and predict the performance of their assets effectively.
An asset level Digital Twin parses and processes real time data streamed directly from the real world so as to create a dynamic, virtual, representation of the equipment being simulated. By creating a Digital Twin, it is possible to gather insight about potential ways to improve operations, increase efficiency or determine potential breakdown points before events happen. Lessons can be learnt from the Digital Twin which can be later applied to the real life installation, reducing process-related incidents and avoiding unplanned downtime, mitigating risk and associated costs, in consequence.
We introduce the Digital Twin paradigm in the following stages:
- Design: Simulation and visualization during the design phase can be used to verify and inspect the overall 3D design and make sure all parts fit together. The design review process can be undertaken remotely together with the client and/or end user to ensure that the design is deemed to be fit for purpose, in a virtual reality environment.
- System integration: 3D visualizations on a system level can verify constraints such as spatial footprint and physical connections. We can integrate the 3D model in a virtual reality environment together with a set of cloud scan data taken from the real life installation, allowing for the aforementioned verifications. Integration effort onsite and the associated downtime for the customer is reduced, as feasibility of installation can be verified beforehand at the virtual environment.
- Diagnostics: Observation of the digital twin, for example in a 3D visualization, can support troubleshooting. Augmented reality devices can provide field technicians with an overlay over the real equipment enabling the visualization of key operational parameters. Simulations can add non-observable data, such as key performance data of non-accessible parts.
- Prediction: Past and present operational and sensor data in combination with predictive algorithms provide insights into the condition of equipment and the likelihood of different failure modes. This helps plan rational maintenance and reduce unplanned downtime.
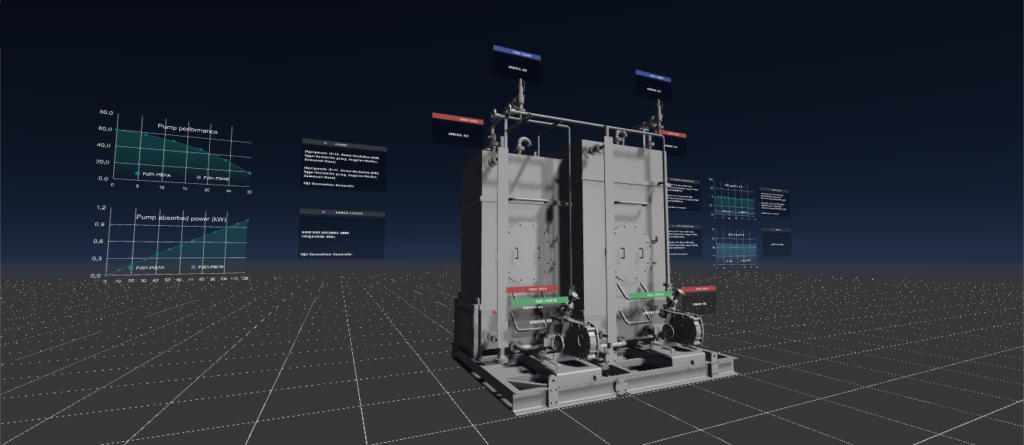
We have developed a Digital Twin model capable of pairing virtual and real equipment, including sensor readings. The most significant features are as follows:
- Fully integrated on a virtual reality (VR) environment.
- Integration of as-built 3D models of equipment from different CAD packages, together with point cloud scan data on a seamless environment.
- Integration of real time data from live SCADA systems or data sets enabling the presentation of real-time status and operating condition, including alarms.
- Integration and visualization of SQL databases of equipment, including equipment and part datasheets, maintenance logs, etc.
- Capable of connecting remotely with users, allowing for remote design reviews and/or remote collaboration thorough the life cycle of the equipment or installation.
Key functionalities include:
- Real-Time Monitoring: Sensors installed on physical assets feed real-time data into the digital model, enabling precise condition monitoring and performance tracking.
- Predictive Analytics: By analyzing historical and live data, Digital Twins can predict potential failures or inefficiencies, allowing proactive maintenance and reducing downtime.
- Simulation and Optimization: Digital Twins enable operators to simulate various scenarios to understand the impact of changes in operations or environmental conditions, optimizing performance without physical intervention.
- Lifecycle Management: From design to decommissioning, Digital Twins provide a unified platform to manage the entire lifecycle of assets.
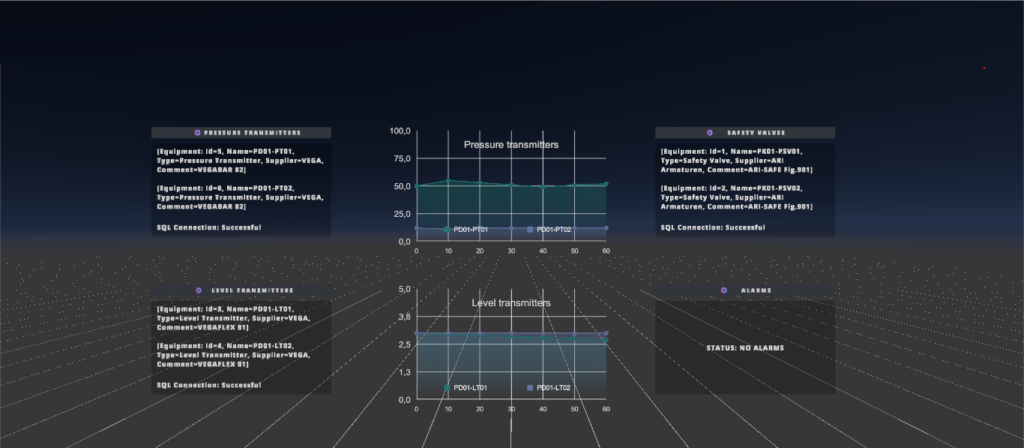
Digital Twin technology offers unparalleled insights into asset performance and operational efficiency. By leveraging real-time data and predictive analytics, safety, sustainability, and profitability can be enhanced while adapting to the challenges of modern energy demands and environmental considerations.
Please follow this link to download our brochure showcasing the creation of an asset level Digital Twin.